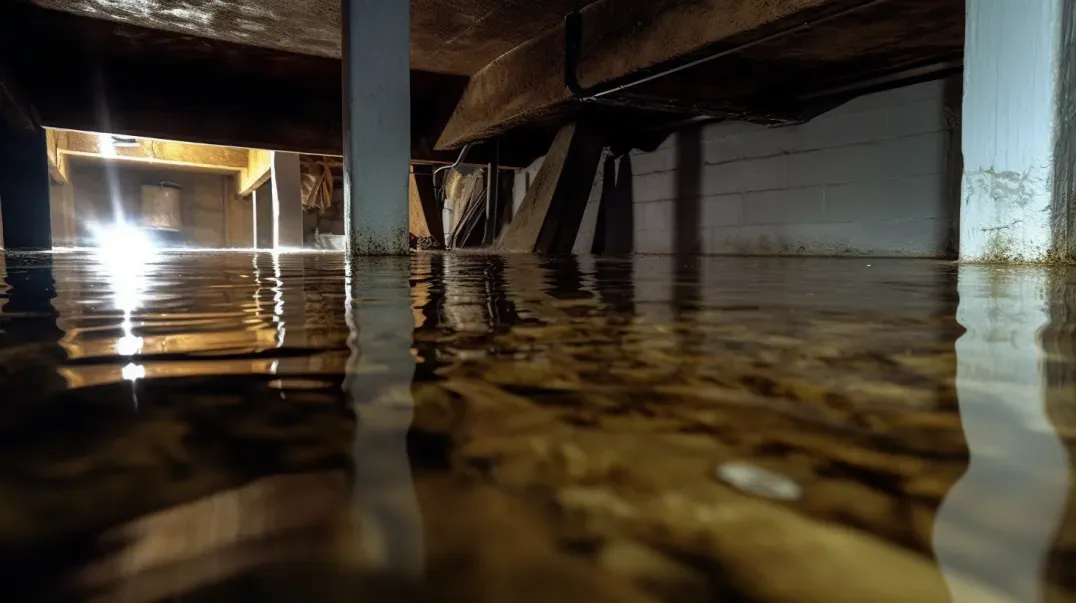
Proper installation of moisture barriers is crucial for ensuring the longevity and energy efficiency of residential and commercial buildings. Moisture barriers are designed to prevent water and vapor from penetrating building materials, which can lead to significant structural damage, mold growth, and compromised insulation effectiveness. When installed correctly, these barriers maintain the integrity of insulation, reduce the load on heating and cooling systems, and contribute to a healthier indoor environment. However, improper installation can negate these benefits, leading to costly repairs and increased energy consumption. This blog explores the critical aspects of moisture barrier installation, highlighting best practices and the impact of meticulous application on energy conservation and building durability. Understanding the importance of proper installation helps homeowners and builders make informed decisions that protect their investments and enhance the performance of their buildings.
Pre-Installation Planning Errors
Inadequate Assessment of Moisture Sources
One of the most critical pre-installation errors in moisture barrier projects is the inadequate assessment of moisture sources. Properly identifying all potential sources of moisture is essential for the effective installation and functionality of moisture barriers.
Importance of Correctly Identifying All Potential Sources of Moisture:
- Failure to thoroughly assess moisture sources can lead to incomplete protection and ongoing issues, such as mold growth, structural damage, and reduced energy efficiency.
- Common sources include groundwater seepage, rainwater infiltration, indoor humidity, plumbing leaks, and condensation. Overlooking any of these can compromise the barrier's effectiveness and the building’s overall health.
Tips for a Comprehensive Assessment:
- Visual Inspections: Conduct thorough inspections of basements, crawl spaces, attics, and other vulnerable areas. Look for signs of water damage, stains, mold, and musty odors.
- Moisture Meters: Use moisture meters to measure the moisture content in walls, floors, and ceilings. This helps in identifying hidden moisture that isn't visible during a visual inspection.
- Thermal Imaging: Employ thermal imaging cameras to detect temperature variations that indicate moisture presence behind walls or under floors.
- Weather Considerations: Consider the local climate and weather patterns. Understanding seasonal variations in humidity and precipitation can help in planning effective moisture control measures.
Choosing the Wrong Type of Moisture Barrier
Selecting the wrong type of moisture barrier is another common pre-installation planning error. Different areas of a home face unique moisture challenges, and using inappropriate materials can fail to address these specific issues.
How Selecting Inappropriate Materials Can Fail to Address Specific Moisture Challenges:
- Each type of moisture barrier—whether vapor barriers, waterproofing membranes, or air barriers—has specific applications and limitations. Using a barrier that isn’t suited to the particular moisture risks can lead to ineffective moisture control and energy inefficiency.
- For instance, using a standard vapor barrier in an area prone to liquid water ingress can result in water bypassing the barrier, leading to structural damage and mold growth.
Guide to Choosing the Right Type of Moisture Barrier for Different Areas of the Home:
Basements:
- Waterproofing Membranes: These are ideal for basements where groundwater and rainwater infiltration are common. They prevent water from seeping through the foundation walls and floors.
- Vapor Barriers: Can be used on interior walls to prevent moisture from migrating into living spaces.
Crawl Spaces:
- Encapsulation Systems: Use a combination of vapor barriers on the ground and waterproofing membranes on the walls to prevent moisture from the soil and exterior environment.
- Ventilation: Ensure proper ventilation to manage humidity levels and prevent condensation.
Attics:
- Vapor Barriers: Install on the warm side of the insulation in cold climates to prevent warm, moist air from reaching the colder attic space.
- Breathable Membranes: These allow moisture to escape while preventing external moisture ingress, crucial for maintaining dry insulation and effective thermal performance.
By understanding and addressing these pre-installation planning errors, homeowners and builders can ensure that moisture barriers are effective in preventing moisture-related issues, protecting the building’s integrity, and enhancing energy efficiency. Proper assessment and material selection are foundational steps in achieving successful moisture management in any construction or renovation project.
Installation Technique Mistakes
Poor Surface Preparation
Proper surface preparation is a critical step in ensuring the effectiveness of moisture barriers. Installing moisture barriers on dirty or unsuitable surfaces can lead to adhesion problems, gaps, and ultimately, the failure of the barrier to protect against moisture.
Consequences of Installing on Dirty or Unsuitable Surfaces:
- Adhesion Issues: Dust, dirt, grease, and other contaminants can prevent the barrier from adhering properly to the surface, leading to bubbles, gaps, and peel-offs.
- Moisture Entrapment: Uneven or unclean surfaces can trap moisture underneath the barrier, which can lead to mold growth and degradation of building materials.
- Reduced Effectiveness: The overall performance of the moisture barrier is compromised, increasing the risk of water penetration and reduced energy efficiency.
Checklist for Surface Preparation Steps:
- Clean the Surface: Thoroughly clean the area where the barrier will be applied. Use a vacuum or a broom to remove loose debris and a damp cloth to wipe away dust and grime. For greasy or oily surfaces, a degreaser may be necessary.
- Dry the Surface: Ensure that the surface is completely dry before installation. Moisture can interfere with the adhesion of the barrier. Use fans or dehumidifiers if necessary to speed up the drying process.
- Smooth the Surface: Repair any cracks, holes, or uneven areas. Use a filler or patching compound to create a smooth, even surface. Sand down rough spots to ensure the barrier can adhere uniformly.
- Prime the Surface: Depending on the type of barrier and surface material, applying a primer may be required. Primers enhance adhesion and provide a suitable bonding surface for the barrier.
Incorrect Application Methods
The correct application of moisture barriers is vital for their performance. Common errors during application, such as improper sealing and insufficient overlap, can significantly reduce the barrier's effectiveness.
Common Errors in Application:
- Improper Sealing: Failing to properly seal edges, seams, and penetrations can allow moisture to bypass the barrier, leading to leaks and condensation issues.
- Insufficient Overlap: Overlapping barrier sheets inadequately can create gaps where moisture can penetrate. The recommended overlap is typically at least 6 inches, but always follow the manufacturer's guidelines.
- Ignoring Manufacturer's Instructions: Each moisture barrier product has specific installation requirements. Ignoring these instructions can result in improper installation and reduced barrier performance.
Step-by-Step Guide to Correct Application:
- Read Manufacturer's Instructions: Before starting, thoroughly read the manufacturer’s installation instructions. These guidelines are tailored to the specific product and ensure optimal performance.
- Measure and Cut: Measure the area to be covered and cut the barrier material accordingly, allowing for the recommended overlap. Cutting the material in advance can streamline the installation process.
- Start from a Corner: Begin applying the barrier from a corner or edge of the surface, ensuring it aligns properly. This helps maintain straight lines and uniform coverage.
- Apply with Consistent Pressure: Use a roller or squeegee to apply the barrier with consistent pressure. This ensures good adhesion and removes air bubbles that can compromise the seal.
- Seal All Seams: Overlap the edges of the barrier sheets by at least 6 inches. Use high-quality sealing tape or adhesive to seal the seams, ensuring there are no gaps.
- Detail Around Penetrations: Carefully seal around any pipes, vents, or other penetrations. Use additional strips of barrier material and sealant to ensure a tight seal around these areas.
- Inspect the Installation: After applying the barrier, inspect the entire area for any gaps, bubbles, or incomplete seals. Address any issues immediately to ensure the barrier is fully effective.
By meticulously preparing surfaces and applying moisture barriers correctly, you can significantly enhance the durability and energy efficiency of your building. Proper installation techniques not only prevent moisture intrusion but also protect the insulation and structural components, ensuring a healthier and more comfortable indoor environment.
Neglecting Climate-Specific Needs
Ignoring Local Climate Factors
The choice and installation of moisture barriers must be tailored to the local climate to ensure optimal performance and energy efficiency. Ignoring local climate factors can lead to ineffective moisture management, compromising the building’s integrity and energy efficiency.
Impact of Climate on Moisture Barriers:
- Humidity Levels: High humidity can increase the risk of mold growth and structural damage, requiring moisture barriers that can handle high moisture content and allow for proper drying.
- Rainfall: Regions with heavy rainfall need robust waterproofing membranes to prevent water penetration, especially in basements and foundations.
- Temperature Variations: Areas with significant temperature fluctuations require barriers that prevent condensation and thermal bridging within walls and insulation.
Examples of Tailoring Installation Practices:
- Humid Climates (e.g., Southeast USA): In these regions, use vapor-permeable barriers on exterior walls to allow moisture to escape while preventing liquid water from entering. Ensure proper ventilation to manage indoor humidity levels.
- Cold Climates (e.g., Northern USA): Install vapor barriers on the interior side of insulation to prevent warm, moist indoor air from condensing on cold exterior walls. Use exterior waterproofing membranes to protect against snow and ice melt.
- Dry Climates (e.g., Southwest USA): While moisture barriers are less critical, focus on areas prone to occasional heavy rains. Use breathable barriers that prevent moisture buildup while allowing vapor diffusion.
Failing to Account for Seasonal Changes
Seasonal variations can significantly affect moisture levels and the performance of moisture barriers. Failing to consider these changes can lead to moisture management issues, reducing the barrier's effectiveness and the building's energy efficiency.
Effects of Seasonal Variations:
- Winter: In cold climates, indoor heating can increase humidity levels, causing condensation issues if moisture barriers are not properly installed. Exterior barriers must handle freeze-thaw cycles without degrading.
- Summer: High outdoor humidity and increased rainfall can lead to higher moisture levels inside buildings. Properly installed barriers must prevent moisture ingress while allowing for adequate drying.
- Spring and Fall: Transitional seasons often bring varying humidity and temperature levels, requiring barriers that can adapt to these changes without losing effectiveness.
Tips for Installing Adaptive Moisture Barriers:
- Flexible Materials: Use moisture barriers made from flexible materials that can expand and contract with temperature changes, maintaining their seal and integrity.
- Ventilation: Ensure that buildings have adequate ventilation to manage varying humidity levels throughout the year. Ventilation systems should complement moisture barriers to prevent condensation and moisture buildup.
- Regular Inspections: Perform seasonal inspections of moisture barriers to check for any damage or degradation caused by changing weather conditions. Address any issues promptly to maintain barrier performance.
- Multi-Layered Systems: Consider multi-layered moisture barrier systems that provide comprehensive protection against various moisture sources and seasonal changes. For example, combining interior vapor barriers with exterior waterproofing membranes can offer robust protection.
By considering local climate factors and seasonal changes, you can ensure that moisture barriers are installed effectively and remain functional year-round. This approach not only protects the building from moisture-related damage but also enhances energy efficiency and indoor comfort, providing a sustainable living or working environment.
Post-Installation Issues
Insufficient Testing and Inspection
Ensuring the integrity of moisture barriers post-installation is crucial for their long-term effectiveness. Insufficient testing and inspection can leave potential issues undetected, leading to moisture intrusion and subsequent damage to the building.
Importance of Post-Installation Testing:
- Verify Integrity: Post-installation testing helps verify that the moisture barrier is installed correctly and that all seams, joints, and penetrations are properly sealed.
- Early Detection: Identifying and addressing issues early can prevent more significant problems such as mold growth, insulation damage, and structural degradation.
- Compliance: Testing ensures that the installation meets building codes and manufacturer specifications, which is essential for warranty validation and building safety.
Recommended Tests and Inspections:
- Visual Inspection: Conduct a thorough visual inspection to check for visible gaps, tears, or loose edges. Pay special attention to seams, corners, and areas around penetrations such as pipes and vents.
- Moisture Meter Testing: Use moisture meters to measure the moisture content in materials adjacent to the barrier. This can help detect any leaks or areas where moisture might be bypassing the barrier.
- Blower Door Test: This test measures the air tightness of the building envelope, helping to identify areas where air (and potentially moisture) is leaking through the barrier.
- Infrared Thermography: Infrared cameras can detect temperature variations that indicate moisture accumulation or thermal bridging, which can compromise the barrier’s effectiveness.
Lack of Maintenance
Regular maintenance is essential to sustain the effectiveness of moisture barriers. Over time, barriers can degrade due to environmental factors, physical damage, or wear and tear. Neglecting maintenance can lead to compromised barriers and increased moisture problems.
Need for Regular Maintenance:
- Prolongs Effectiveness: Routine maintenance ensures that the moisture barrier continues to function as intended, protecting the building from moisture-related issues.
- Prevents Degradation: Regular checks can identify early signs of degradation, allowing for timely repairs and preventing more extensive damage.
- Maintains Energy Efficiency: Effective moisture barriers help maintain insulation performance and reduce HVAC loads, contributing to lower energy costs and improved indoor comfort.
Maintenance Tips for Long-Term Performance:
- Scheduled Inspections: Perform bi-annual or annual inspections to assess the condition of moisture barriers. Focus on high-risk areas such as basements, crawl spaces, and attics.
- Repair Damage Promptly: Address any detected damage, such as tears, gaps, or worn seals, immediately. Use appropriate repair materials to restore the barrier’s integrity.
- Monitor Humidity Levels: Use hygrometers to regularly monitor indoor humidity levels. Consistently high humidity can indicate a problem with the moisture barrier.
- Ensure Proper Ventilation: Maintain proper ventilation in areas prone to moisture accumulation. This helps manage humidity levels and reduces the risk of condensation.
- Check for Mold and Mildew: Look for signs of mold or mildew near the moisture barrier. Their presence can indicate that moisture is bypassing the barrier and requires immediate attention.
- Keep Records: Maintain detailed records of inspections, maintenance activities, and repairs. This documentation can help track the barrier’s performance over time and inform future maintenance needs.
Overlooking Safety and Regulatory Compliance
Safety Hazards During Installation
Installing moisture barriers, while crucial for the protection and energy efficiency of buildings, involves various safety risks that must be managed to protect both homeowners and installation crews.
Potential Safety Risks:
- Falls: Installing moisture barriers often involves working in high or confined spaces, such as attics and crawl spaces, which can increase the risk of falls.
- Exposure to Hazardous Materials: Some moisture barrier materials and adhesives may contain chemicals that can be harmful if inhaled or if they come into contact with skin.
- Electrical Hazards: Working around existing wiring, particularly in basements and attics, poses a risk of electrical shock if proper precautions are not taken.
- Tool-Related Injuries: The use of sharp tools and heavy equipment can lead to cuts, bruises, or more severe injuries if not handled correctly.
Safety Protocols to Follow:
- Personal Protective Equipment (PPE): Ensure that all workers wear appropriate PPE, including gloves, safety goggles, masks, and hard hats, to protect against chemical exposure, dust inhalation, and physical injuries.
- Proper Lighting: Ensure that work areas are well-lit to prevent accidents caused by poor visibility.
- Fall Protection: Use ladders and scaffolding properly, and where necessary, employ safety harnesses and guardrails to prevent falls.
- Electrical Safety: Shut off power to the area where work is being conducted. Use insulated tools and be cautious around wiring and outlets.
- Training: Ensure that all personnel are adequately trained in the use of tools and the handling of materials. Regular safety briefings can reinforce safe practices.
- Ventilation: Maintain proper ventilation in confined spaces to avoid inhaling harmful fumes from adhesives or barriers.
Non-compliance with Building Codes
Adhering to local building regulations and standards is essential to ensure the safety, legality, and performance of moisture barrier installations. Non-compliance can lead to severe consequences, including fines, increased liability, and compromised building integrity.
Risks of Non-compliance:
- Legal and Financial Penalties: Failing to comply with building codes can result in fines, legal action, and increased insurance premiums.
- Structural Issues: Non-compliance can lead to improper installation, which might compromise the building’s structural integrity and performance.
- Safety Hazards: Ignoring regulations can introduce safety risks, such as inadequate fire resistance or improper handling of hazardous materials, endangering occupants.
Ensuring Compliance:
- Understand Local Codes: Familiarize yourself with local building codes and regulations relevant to moisture barrier installation. This includes understanding requirements for materials, installation techniques, and safety standards.
- Consult Professionals: Work with certified contractors and professionals who are knowledgeable about local regulations and have a track record of compliance.
- Obtain Permits: Ensure that all necessary permits are obtained before beginning installation. This often involves submitting plans and receiving approval from local building authorities.
- Inspections: Arrange for inspections by local building officials at key stages of the installation process. This helps ensure that the work meets all regulatory standards and is executed correctly.
- Documentation: Keep detailed records of all compliance-related activities, including permits, inspections, and contractor certifications. This documentation can be crucial if any issues arise in the future.
FAQs
Contact Bull City Crawlspace Today!
Bull City Crawlspace will do everything we can to ensure your experience with us is excellent.
Request A FREE Estimate
Request a Free Estimate Form
Checkout Recent Post
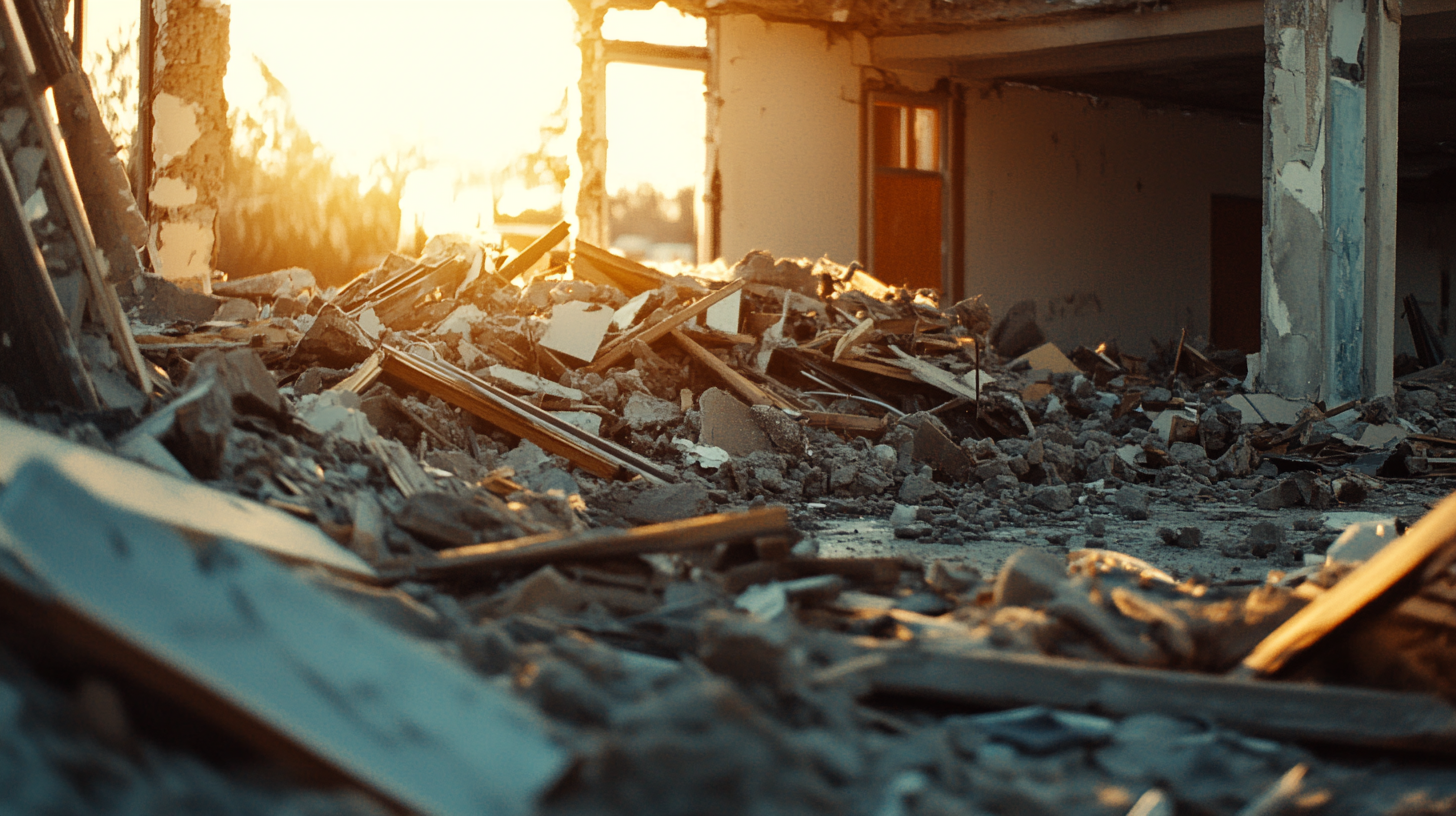
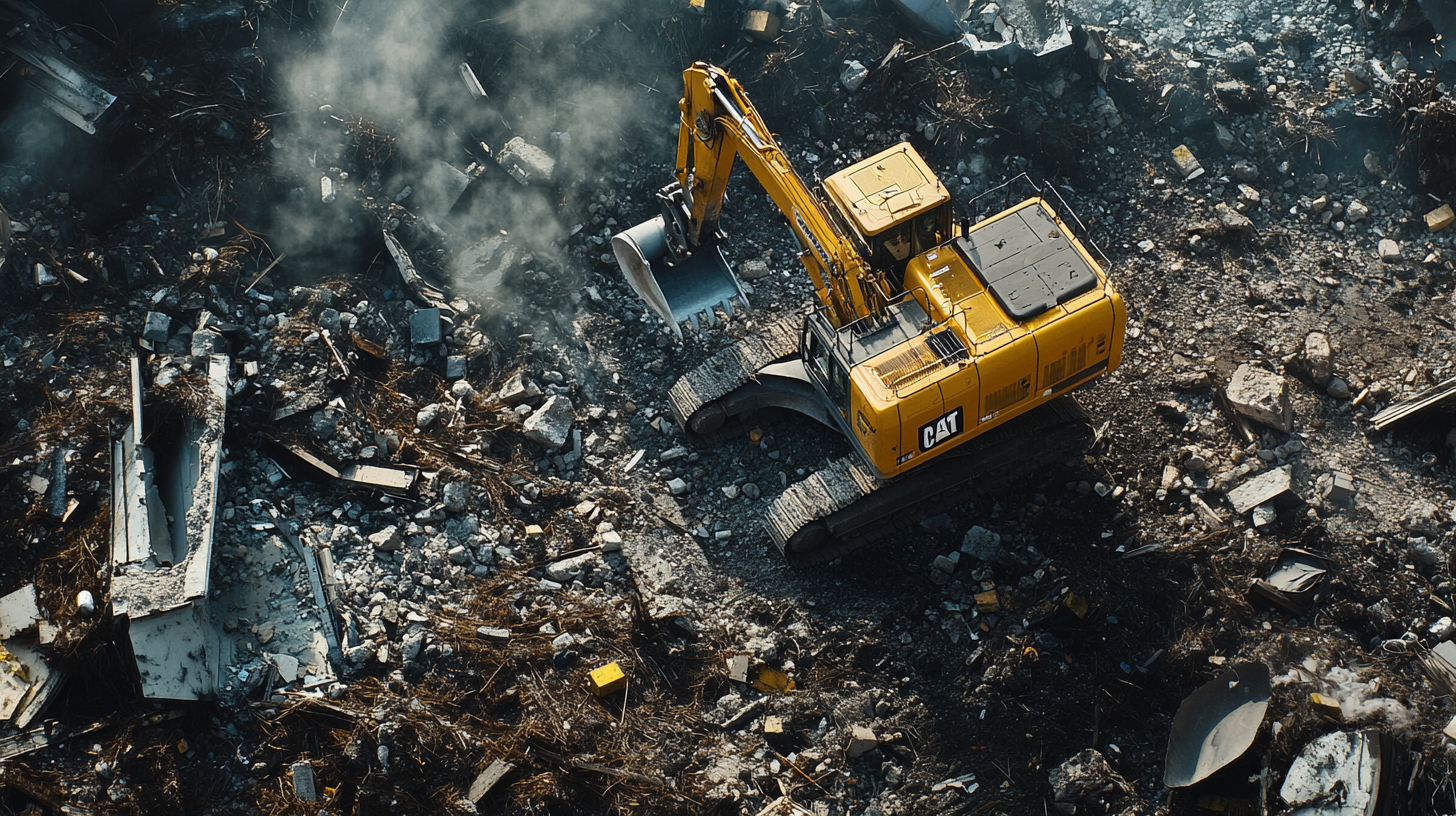


Got a Question? We’re Here to Help.
You can arrange an appointment or make an enquiry by phone or email, orget in touch to us via our contact form.