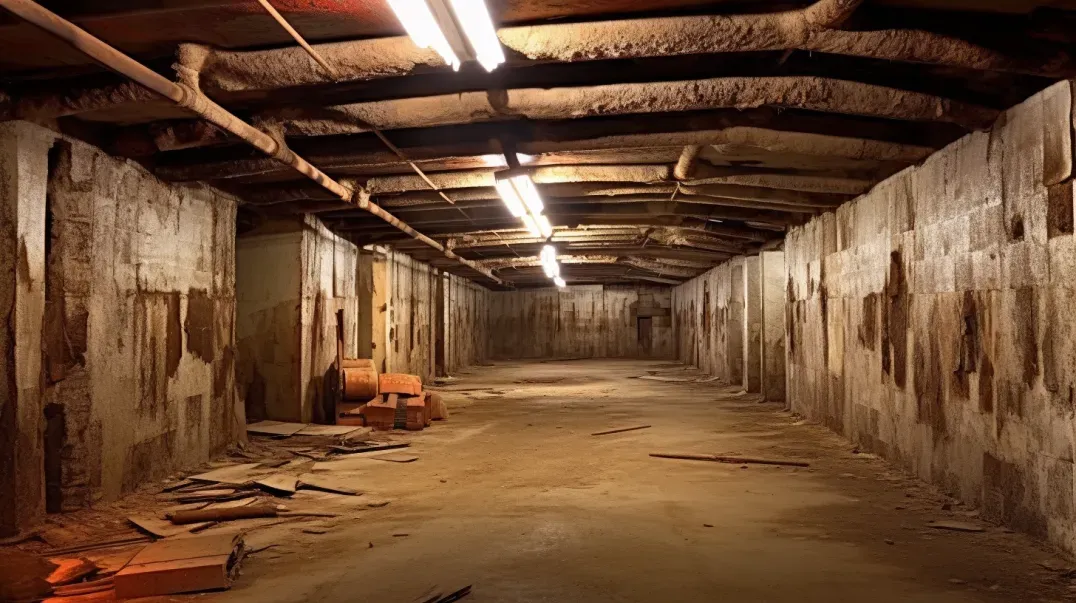
Maintaining a healthy indoor environment in buildings is not just about controlling temperature and ensuring proper ventilation it's also critically dependent on effectively regulating moisture and vapor. The presence of uncontrolled moisture and vapor within building structures can lead to a host of problems that compromise both the integrity of the building and the health of its occupants.
This blog post explores why moisture and vapor control is paramount in any residential or commercial construction. From preventing the structural degradation associated with water infiltration to combating the growth of mold and mildew that can adversely affect indoor air quality, the management of moisture levels holds a key to prolonging the lifespan of building materials and ensuring a safe, comfortable living and working environment.
We will delve into how moisture enters buildings, the risks associated with excessive moisture, and the strategies employed to keep moisture and vapor levels within safe and manageable limits. Join us as we uncover the unseen, yet crucial aspects of building maintenance and wellness that are essential for any sturdy, durable structure.
Understanding Moisture and Vapor in Buildings
Proper management of moisture and vapor is crucial for maintaining the structural integrity and healthiness of indoor environments in buildings. This section of our blog dives deep into the dynamics of how moisture interacts with building materials and the air within, as well as the potential consequences of failing to control these elements effectively.
Basics of Moisture Dynamics
Moisture dynamics within a building involve complex processes that can significantly impact the building's condition and the comfort of its occupants.
- How Moisture Moves Through Buildings: Moisture can enter buildings in several ways, including direct leakage through roofs and walls, diffusion through materials, and as a byproduct of indoor activities like cooking and showering. Once inside, moisture moves through the building via air currents, diffuses through materials, or is driven by differences in water vapor pressure.
- Difference Between Moisture in Liquid Form and as Vapor: Moisture in buildings primarily exists in two forms liquid and vapor. Liquid moisture includes visible water, such as leaks or condensation on surfaces, which can directly damage materials. Vapor, however, refers to water in its gaseous state, which can permeate materials more subtly and often goes unnoticed until problems like mold or structural weakening become apparent.
Impact of Uncontrolled Moisture and Vapor
The control of moisture and vapor within a building is not just a matter of preventing discomfort but is essential for avoiding serious structural and health issues.
- Potential Structural Damage from Moisture and Vapor: Excessive moisture can lead to the deterioration of building materials, including rot in wooden structures, corrosion in metal components, and the delamination of laminated materials. Vapor that condenses into water within the building structure can freeze and expand, causing cracking and other structural damage over time.
- Health Risks Associated with Poor Moisture and Vapor Control: Inadequate management of moisture levels can create environments conducive to mold and mildew growth, which are known to cause respiratory problems, allergies, and other health issues. High humidity levels can also increase the off-gassing of volatile organic compounds (VOCs) from materials such as paints and furnishings, further compromising indoor air quality.
Defining Moisture Barriers and Vapor Barriers
Understanding the distinctions and functions of moisture barriers and vapor barriers is crucial for effective building construction and maintenance. These barriers are designed to protect structures from moisture-related damage but serve different purposes and are implemented in different ways depending on their specific roles.
What is a Moisture Barrier?
A moisture barrier is a protective layer installed in buildings to prevent liquid water from penetrating and damaging the structure. It acts as a critical line of defense against moisture that can lead to structural decay, mold growth, and reduced insulation effectiveness.
- Main Functions of Moisture Barriers: The primary function of a moisture barrier is to block water from outside sources, such as rain or groundwater, from entering a building. This protection helps maintain the structural integrity of the building and improves indoor comfort and air quality by preventing dampness and mold.
- Common Materials and Locations for Moisture Barrier Applications: Moisture barriers are commonly made from materials like polyethylene sheeting, rubber membranes, and treated papers. These barriers are typically installed in areas prone to high moisture exposure, such as foundation walls, basements, and crawl spaces, to ensure a dry and stable building environment.
What is a Vapor Barrier?
A vapor barrier, by contrast, is designed to prevent the diffusion of water vapor that could condense within the building envelope, potentially leading to moisture problems inside the structure.
- Main Functions of Vapor Barriers: Vapor barriers help control the amount of moisture passing through walls, ceilings, and floors by diffusion. They are crucial for preventing water vapor from condensing into liquid water within the building envelope, which is vital for preventing mold growth and insulation damage.
- Typical Materials Used for Vapor Barriers and Where They Are Installed: Materials commonly used for vapor barriers include plastic sheets, foil-backed paper, and specialized paint coatings. Vapor barriers are often installed in walls, attics, and crawl spaces, especially in climates with cold winters or very humid conditions, to manage interior humidity levels effectively.
Key Differences Between Moisture Barriers and Vapor Barriers
Understanding the distinctions between moisture barriers and vapor barriers is essential for any construction or renovation project. These barriers, while often confused, serve different protective functions and have different requirements for material properties, application, and installation.
Material Properties and Permeability
Moisture barriers and vapor barriers differ significantly in their material composition and permeability, which directly affects their functions within a building’s structure.
- Material Composition and Permeability: Moisture barriers are typically made from impermeable or very low-permeability materials such as plastic films, rubber membranes, or coated fabrics designed to prevent liquid water from passing through. Vapor barriers, on the other hand, are made from materials that may also be impermeable but are primarily chosen for their ability to prevent the diffusion of water vapor, such as polyethylene sheets, foil-faced paper, or vapor-retardant paints.
- How Properties Affect Functions: The choice of material affects the barrier's function. Moisture barriers need to withstand hydrostatic pressure from liquid water, often found in ground contact areas like basements. Vapor barriers are used primarily in interior applications, such as in walls or roofs, to manage the diffusion of moisture from inside to outside, preventing condensation within the building envelope.
Application and Installation
The effectiveness of both moisture barriers and vapor barriers greatly depends on their correct application and installation within the building structure.
- Guidelines on Application and Installation: Moisture barriers should be applied in areas susceptible to liquid water exposure, such as at the foundation level, beneath siding, or along basement walls. Vapor barriers are best installed in locations prone to high humidity levels, such as in attic floors under insulation to prevent warm indoor air from condensing in the cold zones.
- Importance of Proper Installation: Proper installation is crucial for the functionality of both types of barriers. For moisture barriers, this means ensuring coverage continuity, overlapping seams by a recommended amount, and sealing around penetrations to prevent water ingress. For vapor barriers, ensuring that the barrier is completely sealed and covers all potential points of moisture intrusion is critical. Breaks or gaps in the barrier can lead to condensation problems, potentially compromising the building's structural integrity and interior air quality.
Choosing the Right Barrier for Your Project
Selecting the appropriate barrier for moisture and vapor control is critical to the long-term success and functionality of your building project. This choice depends on a variety of factors including climate, building design, and the specific function of the spaces involved. Here we discuss the key considerations and provide real-world examples to guide your decision-making process.
Factors to Consider
When choosing between a moisture barrier and a vapor barrier, several factors need to be carefully evaluated to ensure optimal performance and durability:
- Climate and Environmental Considerations: The local climate is a critical determinant in barrier selection. For example, in areas with high humidity and heavy rainfall, a robust moisture barrier is necessary to prevent water intrusion. Conversely, in cold climates, a vapor barrier is essential to prevent condensation within walls, which can degrade building materials and insulation.
- Building Design and Specific Use Areas: The design of the building and the specific functions of different areas also influence the choice of barriers. Moisture barriers are crucial in basements and other ground-contact areas where water ingress is a potential problem. Vapor barriers are more pertinent in areas like attics and walls that are susceptible to condensation risks due to temperature differences.
Case Studies
Understanding the practical application of these barriers can be further illuminated by examining real-life scenarios:
- Scenario Where a Moisture Barrier is Preferred:
- Case Study: In a coastal city known for its stormy weather, a newly constructed community center faced significant issues with water seepage in its basement. After retrofitting with a high-density polyethylene moisture barrier, the problem was resolved, protecting the foundation from further water damage and mold growth.
- Scenario Where a Vapor Barrier is Preferred:
- Case Study: In a residential project in a northern climate, homeowners experienced seasonal condensation inside their walls, leading to insulation dampness and thermal loss. The installation of a continuous interior vapor barrier during a renovation project dramatically reduced condensation and improved the efficiency of the home’s heating system.
- Lessons Learned from Real-Life Applications:
- The importance of assessing both the environmental conditions and the specific needs of the building cannot be overstated. Proper assessment and professional consultation saved these projects from recurring issues and extensive subsequent repairs.
- Another lesson is the critical nature of installation quality. Even the best-suited barrier can fail if not installed correctly, emphasizing the need for skilled installation and meticulous attention to detail during the application process.
Common Installation Mistakes and How to Avoid Them
Installing moisture and vapor barriers correctly is crucial to their effectiveness. Mistakes during installation can lead to significant long-term problems, including structural damage and poor indoor air quality. This section identifies common errors made during the installation of moisture and vapor barriers and offers best practices to ensure their optimal performance.
Moisture Barrier Mistakes
The correct installation of moisture barriers is vital to prevent water ingress that could lead to damp issues and structural decay.
- Typical Errors Made During Installation:
- Inadequate Overlap: Not overlapping the sheets sufficiently is a common error that can lead to gaps and water seepage.
- Poor Sealing at Joints: Failing to seal joints properly between the barrier sheets and around penetrations (like pipes and cables) compromises the barrier's effectiveness.
- Incorrect Material Choice: Using materials that are not suitable for the specific environmental conditions or building type can render the barrier ineffective.
- Best Practices for Ensuring Moisture Barriers Perform as Expected:
- Ensure overlaps are at least 6 inches and use a high-quality sealant or tape specifically designed for moisture barriers to seal all seams and joints.
- Choose the correct type of moisture barrier material based on the local climate, soil conditions, and the specific requirements of the building area.
- Conduct a thorough pre-installation inspection to ensure the surface is clean and smooth, and make any necessary repairs to the foundation or walls before installing the barrier.
Vapor Barrier Mistakes
Vapor barriers help control the diffusion of moisture to prevent condensation within the building envelope, which is crucial in cold climates.
- Common Pitfalls in the Installation of Vapor Barriers:
- Incorrect Placement: Installing vapor barriers on the wrong side of the insulation material can trap moisture, leading to condensation and potential mold growth.
- Incomplete Coverage: Failing to cover all areas, including corners and edges, can allow moisture to bypass the barrier.
- Using Permeable Materials: Selecting materials that are too permeable for the climate zone can fail to prevent moisture transmission effectively.
- Tips for Effective Vapor Barrier Installation:
- Always install the vapor barrier on the warm side of the insulation (towards the interior in cold climates) to prevent warm moist air from reaching colder surfaces.
- Ensure the vapor barrier covers all surfaces without any gaps. Use appropriate tapes and sealants to bond seams, around outlets, and at perimeters.
- Consult building codes and standards for your specific climate zone to select a vapor barrier with the appropriate permeability.
FAQs
Contact Bull City Crawlspace Today!
Bull City Crawlspace will do everything we can to ensure your experience with us is excellent.
Request A FREE Estimate
Request a Free Estimate Form
Checkout Recent Post
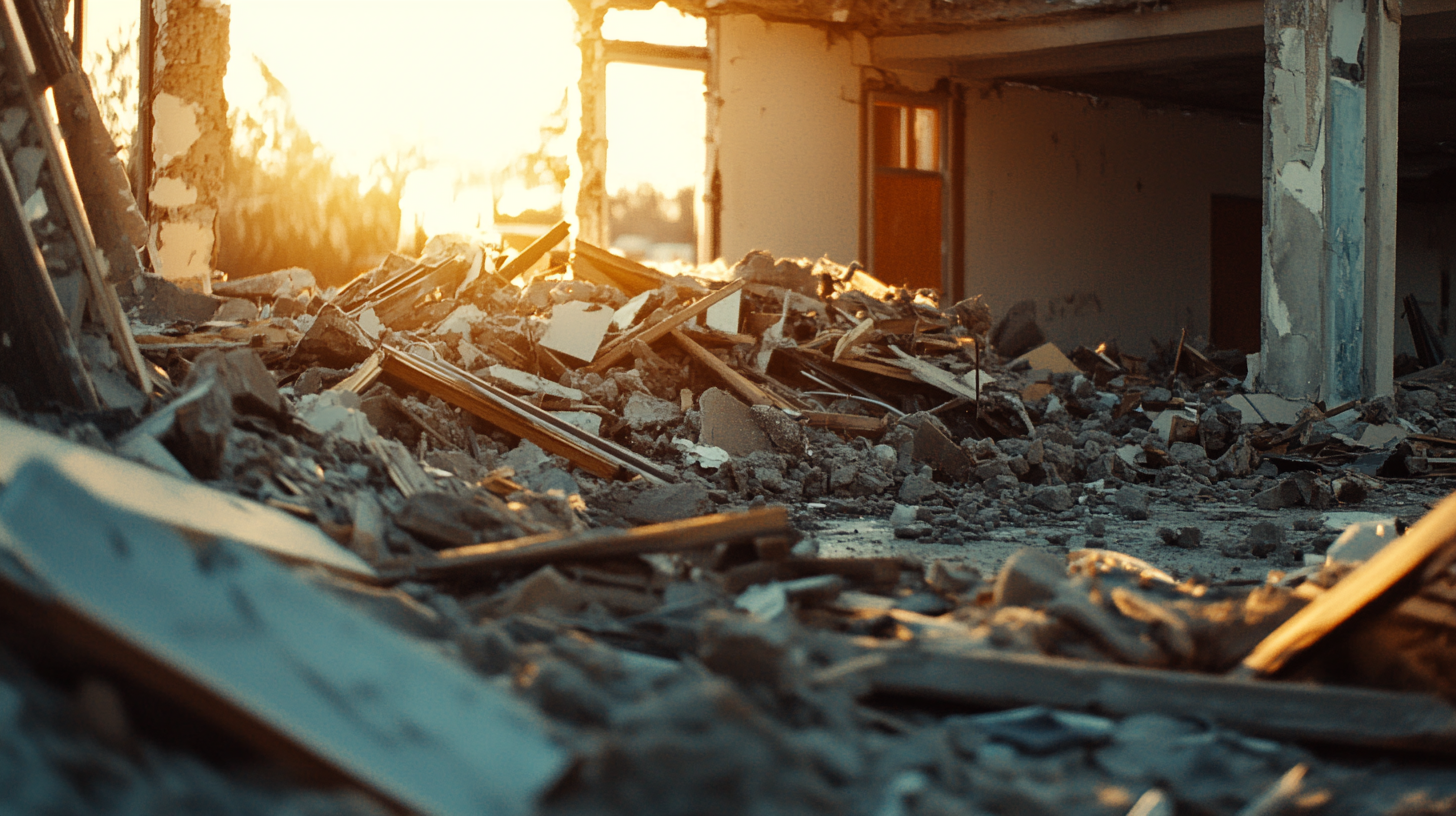
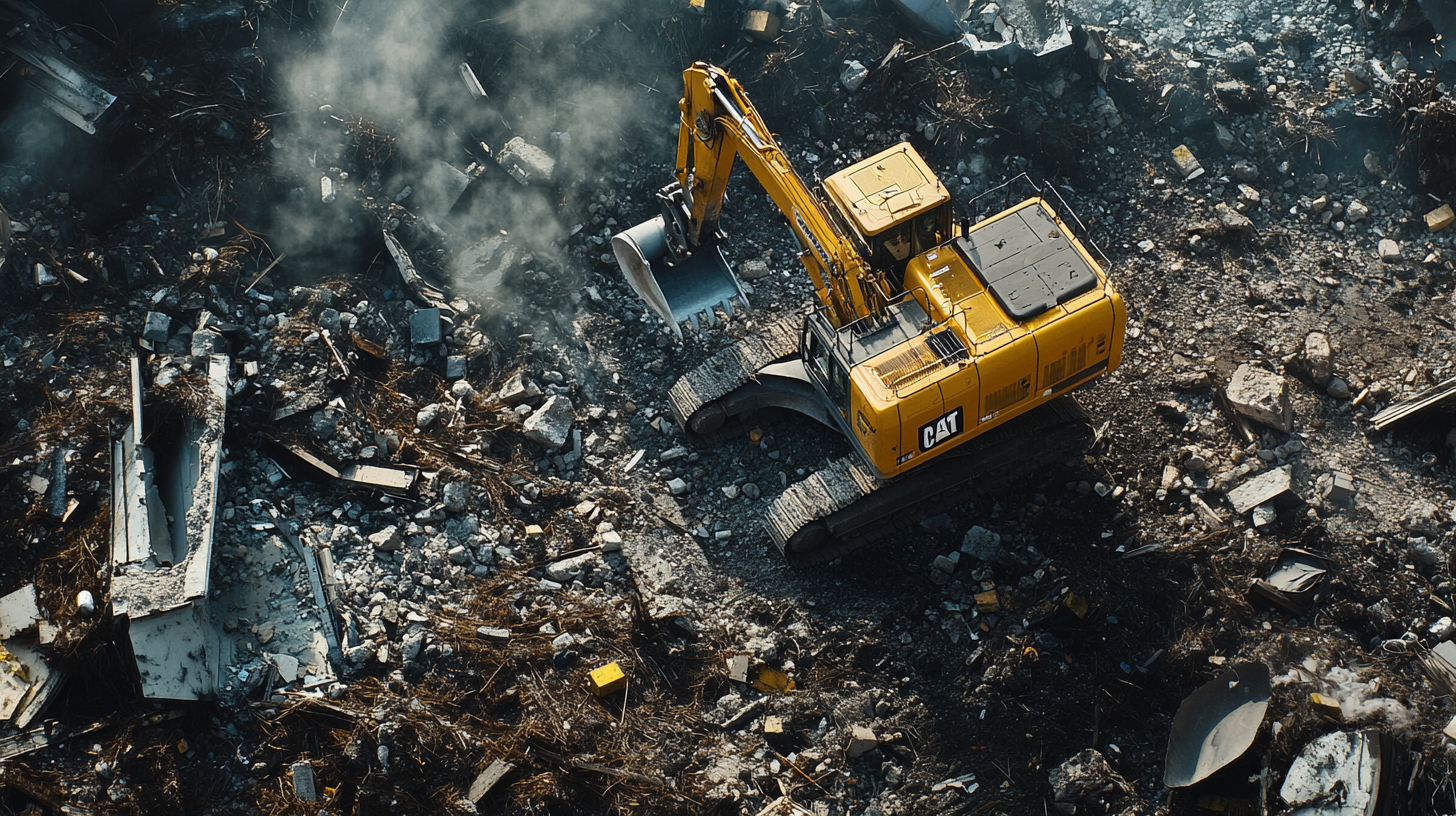


Got a Question? We’re Here to Help.
You can arrange an appointment or make an enquiry by phone or email, orget in touch to us via our contact form.