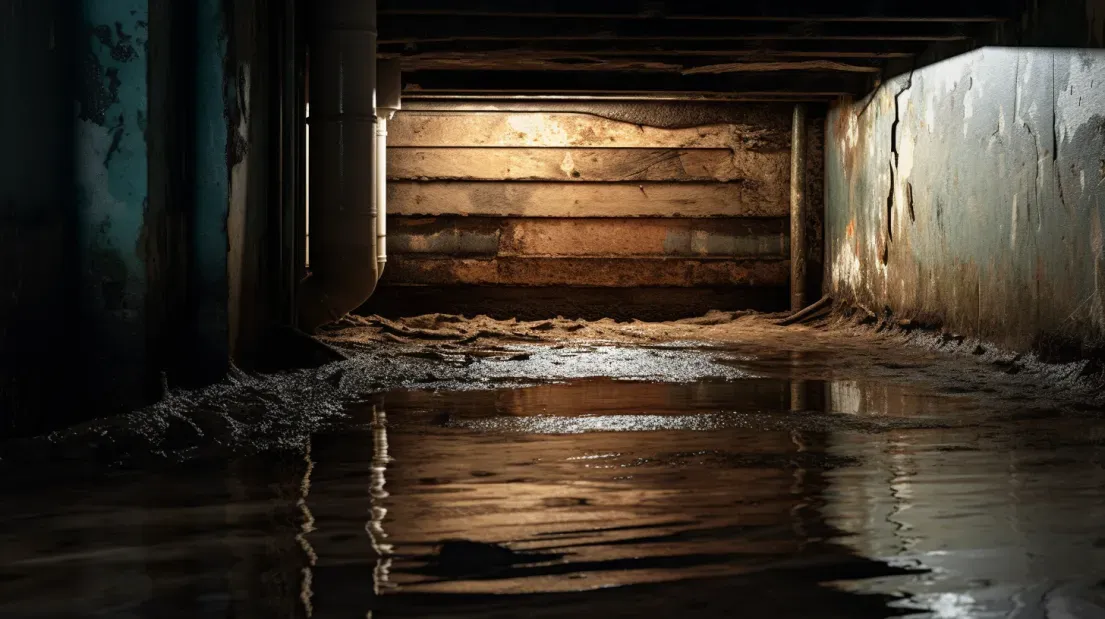
The versatility and significance of annotation and marking systems extend across a multitude of industries, including construction, packaging, and beyond. These systems serve as critical tools for ensuring accuracy, compliance, and efficiency. In the construction industry, annotations play a pivotal role in maintaining clear communication and documentation, which is essential for project management, safety, and adherence to regulatory standards. Similarly, in the packaging industry, precise labeling and annotations are crucial for inventory management, logistics, and regulatory compliance, ensuring that products are handled and transported correctly.
The foundational guidelines and principles outlined emphasize the importance of consistency, clarity, and accuracy in annotations, which are indispensable across these sectors. They stress the need for standardized practices that can be universally understood and applied, minimizing the risk of errors and enhancing operational efficiency. Whether it is through digital or physical means, the implementation of these principles ensures that all stakeholders have access to the critical information necessary to perform their tasks effectively and safely.
By adhering to these guidelines, industries not only improve their internal processes but also enhance overall communication and collaboration. This fosters a more cohesive and efficient working environment, where every detail is meticulously recorded and easily accessible, thereby supporting the seamless execution of complex projects and operations.
Understanding Moisture Barriers
What are Moisture Barriers?
Definition and Types Moisture barriers are essential components designed to prevent the penetration and accumulation of moisture within structures and materials. They come in various forms, including vapor barriers, liquid-applied barriers, and sheet membranes, each tailored to specific applications and environmental conditions.
Common Materials Used The effectiveness of moisture barriers largely depends on the materials used. Commonly utilized materials include polyethylene, known for its durability and resistance to water; rubber, which offers flexibility and strong sealing properties; and asphalt, valued for its robust waterproofing capabilities. These materials are chosen based on their ability to provide reliable moisture protection in diverse settings.
Functionality of Moisture Barriers
Mechanisms of Action Moisture barriers operate by creating a physical obstruction that prevents water vapor and liquid water from infiltrating protected areas. This functionality is critical in maintaining structural integrity and preventing damage caused by moisture-related issues such as mold, mildew, and material degradation.
Applications in Different Sectors The application of moisture barriers spans various industries, including construction, packaging, and manufacturing. In construction, they are integral to building envelopes, protecting walls, floors, and roofs. In packaging, moisture barriers preserve product integrity during storage and transportation, particularly for moisture-sensitive goods.
Climate Variables Affecting Moisture Barriers
Temperature
- High Temperatures High temperatures can impact the performance of moisture barriers by affecting their material properties, such as melting points and flexibility. For example, polyethylene may soften or deform under extreme heat, compromising its effectiveness. Case studies have shown that protective measures, such as using UV-resistant coatings, can mitigate these effects.
- Low Temperatures Conversely, low temperatures can make materials brittle, increasing the risk of cracking and failure. Rubber-based barriers, for instance, may lose their elasticity and become prone to damage in freezing conditions. Real-world examples highlight the need for materials specifically engineered to withstand cold environments.
Humidity
- High Humidity Levels High humidity can accelerate the absorption of moisture by some materials, potentially leading to mold and mildew growth. Effective moisture barriers are designed to resist high humidity by maintaining low permeability. In regions with consistently high humidity, the selection of appropriate barrier materials is crucial to prevent such issues.
- Low Humidity Levels Low humidity can cause drying effects and material shrinkage, which may lead to gaps and breaches in the moisture barrier. This can compromise the barrier's integrity and allow moisture penetration. Examples of performance failures in low-humidity environments emphasize the importance of regular inspection and maintenance.
Precipitation
- Rainfall Direct exposure to rainfall poses a significant challenge to moisture barriers, particularly in roofing and exterior wall applications. Protective measures, such as proper installation techniques and the use of drainage systems, are vital. Case studies demonstrate successful strategies for managing heavy rainfall and preventing water ingress.
- Snow and Ice Freeze-thaw cycles associated with snow and ice can cause moisture barriers to expand and contract, potentially leading to cracks and leaks. Strategies for mitigation include the use of flexible materials that can accommodate these cycles and the application of additional protective layers.
Wind
- Wind Speed and Direction Wind can exert pressure differences on structures, testing the integrity of moisture barriers. High wind speeds and specific wind directions can lead to physical damage or breaches. Examples of wind damage highlight the need for robust design and installation practices to ensure barrier stability under varying wind conditions.
By adhering to the foundational guidelines and principles, industries can enhance the
performance and reliability of moisture barriers, ensuring long-term protection against the detrimental effects of moisture.
Regional Climate Considerations
Tropical Climates
High Temperature and Humidity Impacts Tropical climates are characterized by consistently high temperatures and humidity levels, which pose unique challenges for moisture barriers. The combination of heat and moisture can lead to accelerated material degradation, including swelling, warping, and loss of structural integrity. These conditions necessitate the use of highly durable materials that can withstand such environments without compromising their effectiveness.
Specific Challenges and Solutions In tropical regions, moisture barriers must be designed to resist both high humidity and intense solar radiation. Materials such as UV-resistant polyethylene and specially formulated rubber compounds are ideal for these conditions. Additionally, implementing ventilation systems and using reflective coatings can help mitigate the effects of heat and humidity on building structures.
Arid Climates
Low Humidity and High Temperature Effects Arid climates, characterized by low humidity and high temperatures, can lead to different sets of challenges. The lack of moisture can cause some materials to dry out and become brittle, leading to cracks and gaps in the moisture barriers. High temperatures can exacerbate these issues, causing thermal expansion and contraction that further stress the materials.
Adaptations for Dry Environments To address the challenges of arid climates, moisture barriers should be constructed from materials that maintain flexibility and resilience in dry conditions. Asphalt-based barriers, for example, can provide effective protection without becoming brittle. Incorporating thermal insulation and using materials with low thermal expansion coefficients are also crucial adaptations for maintaining barrier integrity.
Temperate Climates
Seasonal Variations and Their Influence Temperate climates experience significant seasonal variations, with changes in temperature and humidity throughout the year. These fluctuations can impact the performance of moisture barriers, as materials must adapt to both warm, humid summers and cold, dry winters. This requires a versatile approach to barrier design and material selection.
Case Studies from Temperate Regions In temperate regions, successful moisture barrier applications often involve multi-layer systems that provide year-round protection. Case studies have shown that combining vapor barriers with breathable membranes can effectively manage seasonal moisture levels while maintaining energy efficiency. Regular maintenance and inspections are also key to ensuring long-term performance.
Cold Climates
Extreme Cold and Snow Impacts Cold climates pose significant challenges due to extreme temperatures and the presence of snow and ice. These conditions can cause moisture barriers to become brittle and susceptible to cracking. Additionally, freeze-thaw cycles can lead to the formation of ice within barrier materials, causing further damage and potential breaches.
Design Considerations for Cold Regions In cold climates, moisture barriers need to be designed for flexibility and resistance to freezing temperatures. Materials such as flexible asphalt membranes and specialized rubber compounds are effective in these environments. Incorporating insulation layers and ensuring proper drainage to manage snow and ice melt are critical design considerations. Case studies from cold regions highlight the importance of using barriers that can endure repeated freeze-thaw cycles without losing integrity.
By adhering to the foundational guidelines and principles, industries can develop moisture barriers that are tailored to the specific demands of different regional climates, ensuring long-term durability and effectiveness .
Enhancing Moisture Barrier Performance
Material Innovations
Advances in Moisture Barrier Materials The field of moisture barrier technology has seen significant advancements in recent years, driven by the need for more durable and effective solutions. Innovations have focused on developing materials that offer superior resistance to environmental stressors, improved flexibility, and enhanced longevity. New technologies include high-performance polyethylene blends, advanced rubber formulations, and multi-layer composite materials that combine the strengths of various substances.
Examples of New Technologies Recent developments have introduced materials such as vapor-permeable membranes, which allow for moisture to escape from structures while preventing water ingress. Nanotechnology has also played a role, with nanoparticles being integrated into barrier materials to enhance their properties, such as increased tensile strength and reduced permeability. Additionally, smart materials that can respond to environmental changes, such as self-sealing barriers, are being explored for their potential to provide dynamic protection.
Installation Best Practices
Guidelines for Effective Installation Proper installation is crucial for the effectiveness of moisture barriers. Adhering to best practices ensures that barriers perform as intended and provide long-term protection. Key guidelines include ensuring that the substrate is clean, dry, and free from contaminants before installation. The application of barriers should follow manufacturer specifications, with attention to overlaps, sealing edges, and anchoring methods.
Common Mistakes to Avoid Avoiding common installation mistakes is essential to maintain the integrity of moisture barriers. These mistakes include improper surface preparation, inadequate sealing of seams and joints, and insufficient curing time for liquid-applied barriers. Failure to account for thermal expansion and contraction can also lead to gaps and breaches. Ensuring that installers are well-trained and follow detailed installation procedures can mitigate these risks.
Maintenance and Inspection
Regular Maintenance Routines Regular maintenance is vital to ensure the ongoing performance of moisture barriers. This involves scheduled inspections, cleaning, and repairs as needed. Maintenance routines should include checking for signs of wear and tear, such as cracks, blisters, or delamination, and addressing any issues promptly to prevent further damage.
Inspection Techniques and Tools Effective inspection techniques are necessary to identify potential problems with moisture barriers. Visual inspections should be conducted regularly, supplemented by more advanced methods such as infrared thermography to detect hidden moisture issues. Moisture meters can measure the presence of water within barrier materials, while adhesion tests can assess the bond strength of applied barriers. Utilizing a combination of these tools ensures comprehensive monitoring and helps maintain the barrier's effectiveness over time.
By following the outlined guidelines and principles, industries can significantly enhance the performance and reliability of moisture barriers, ensuring they provide the necessary protection against environmental factors.
Case Studies
Successful Applications
Real-World Examples of Effective Moisture Barrier Performance One exemplary case study involves a commercial building project in a coastal region, where high humidity and frequent rainfall posed significant challenges. The project utilized a multi-layer moisture barrier system consisting of vapor-permeable membranes combined with a robust polyethylene sheet. The installation followed strict adherence to guidelines, including proper substrate preparation and meticulous sealing of seams and joints. As a result, the building has remained free from moisture intrusion for over a decade, demonstrating the effectiveness of the chosen materials and installation practices.
Lessons Learned from Successful Projects From this and other successful projects, several key lessons have emerged. First, selecting the right combination of materials tailored to the specific environmental conditions is crucial. Second, rigorous adherence to installation guidelines ensures long-term performance. Lastly, incorporating regular maintenance and inspection routines can preemptively address potential issues, thereby extending the lifespan of the moisture barriers.
Failures and Lessons Learned
Analysis of Moisture Barrier Failures A notable case of moisture barrier failure occurred in a residential development in a temperate climate zone. The project used a single-layer asphalt barrier which, over time, exhibited signs of cracking and delamination. Upon investigation, it was found that the installation did not adequately account for seasonal temperature fluctuations, and the material used lacked the necessary flexibility to withstand these changes. Additionally, the maintenance routines were irregular, leading to undetected minor damages that eventually compounded into significant issues.
Recommendations for Improvement This failure highlighted several critical areas for improvement. First, it underscored the importance of choosing materials with appropriate flexibility and durability for the specific climate conditions. Second, it emphasized the need for thorough and consistent installation practices, including allowing for thermal expansion and contraction. Finally, it illustrated the necessity of regular and systematic maintenance and inspections to identify and address minor issues before they escalate.
By studying both successful applications and failures, industries can better understand the importance of adhering to established guidelines and principles. These case studies serve as valuable lessons, providing actionable insights to enhance the performance and reliability of moisture barriers across various applications.
Maintenance and Inspection
Regular Maintenance Tips
Inspecting for Damage or Wear Regular inspections are vital to maintaining the effectiveness of moisture barriers. These inspections should be comprehensive, including visual checks for signs of damage such as cracks, blisters, or delamination. Utilizing advanced tools like moisture meters and infrared thermography can help detect hidden issues that are not visible to the naked eye. Conducting these inspections routinely, such as bi-annually or after significant weather events, ensures that any emerging problems are identified early.
Repairing Small Issues Before They Escalate Addressing minor issues promptly can prevent them from developing into major problems that compromise the entire barrier system. Small cracks or punctures should be repaired using appropriate patching materials that match the original barrier's specifications. It's essential to follow manufacturer guidelines for repairs to ensure compatibility and effectiveness. Regular maintenance routines should also include cleaning debris and ensuring that drainage systems are functioning properly to avoid water accumulation that can damage the barriers.
Long-Term Performance
Factors that Influence the Longevity of Moisture Barriers The long-term performance of moisture barriers is influenced by several factors including the quality of materials used, the conditions of the installation, and the environmental stresses they are exposed to. High-quality materials that are resistant to UV radiation, temperature fluctuations, and mechanical stresses tend to have a longer lifespan. Proper installation techniques, such as ensuring full adhesion and proper overlap of seams, are critical to prevent water ingress and ensure durability.
Tips for Ensuring Long-Term Effectiveness To ensure long-term effectiveness, it is crucial to select materials that are appropriate for the specific environmental conditions of the installation site. This includes considering factors such as temperature extremes, humidity levels, and exposure to UV radiation. Additionally, following best practices for installation, such as using adequate surface preparation, correct application methods, and ensuring all joints and seams are properly sealed, will significantly enhance the longevity of moisture barriers.
Regularly scheduled maintenance and inspections should be part of the overall strategy to ensure the long-term performance of moisture barriers. This includes routine cleaning, immediate repair of any detected damage, and periodic reassessment of the barrier's condition to ensure it continues to meet performance standards. By adhering to these guidelines and principles, the integrity and effectiveness of moisture barriers can be maintained over extended periods, providing reliable protection against moisture intrusion .
FAQs
Contact Bull City Crawlspace Today!
Bull City Crawlspace will do everything we can to ensure your experience with us is excellent.
Request A FREE Estimate
Request a Free Estimate Form
Checkout Recent Post
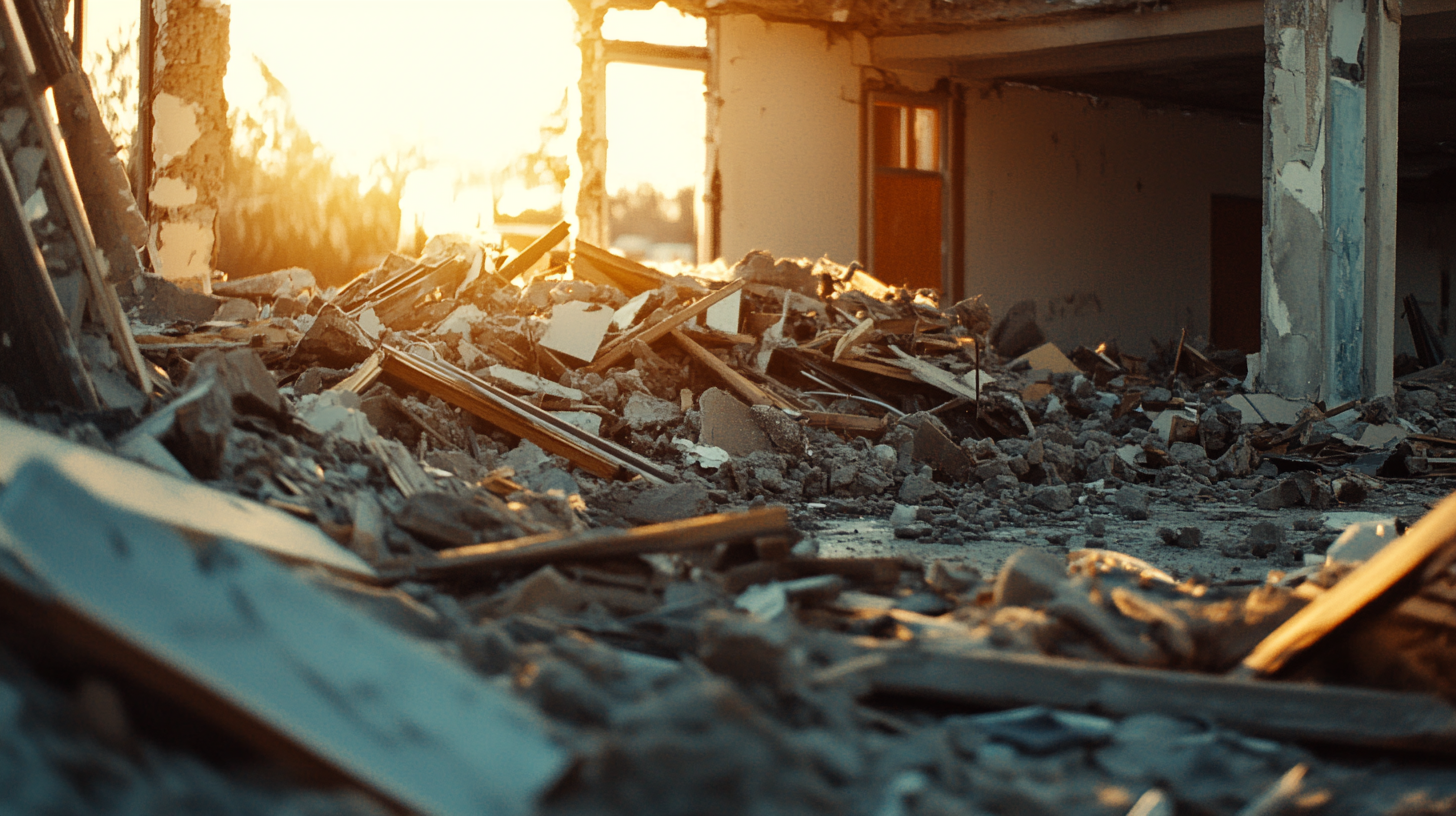
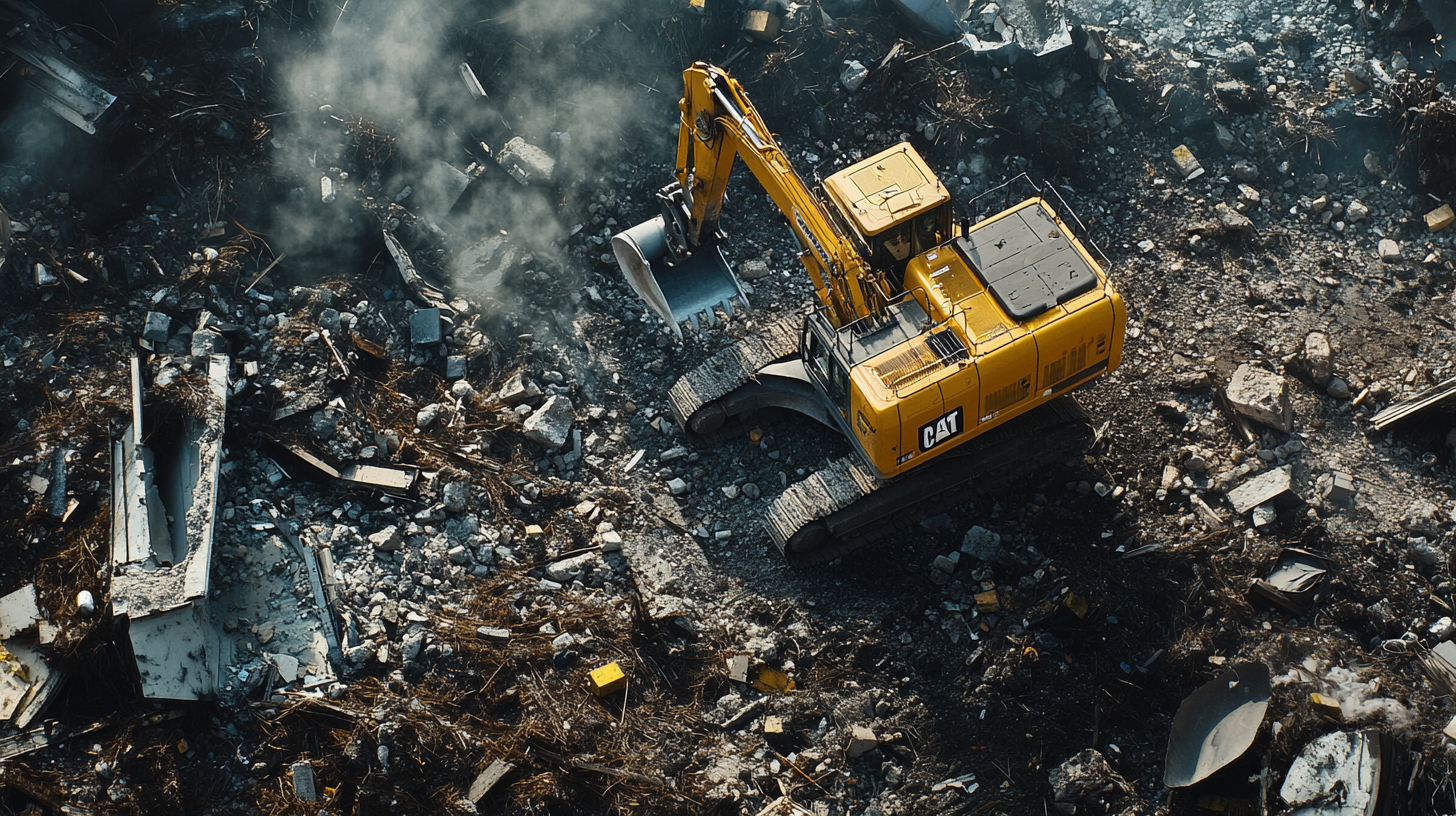


Got a Question? We’re Here to Help.
You can arrange an appointment or make an enquiry by phone or email, orget in touch to us via our contact form.