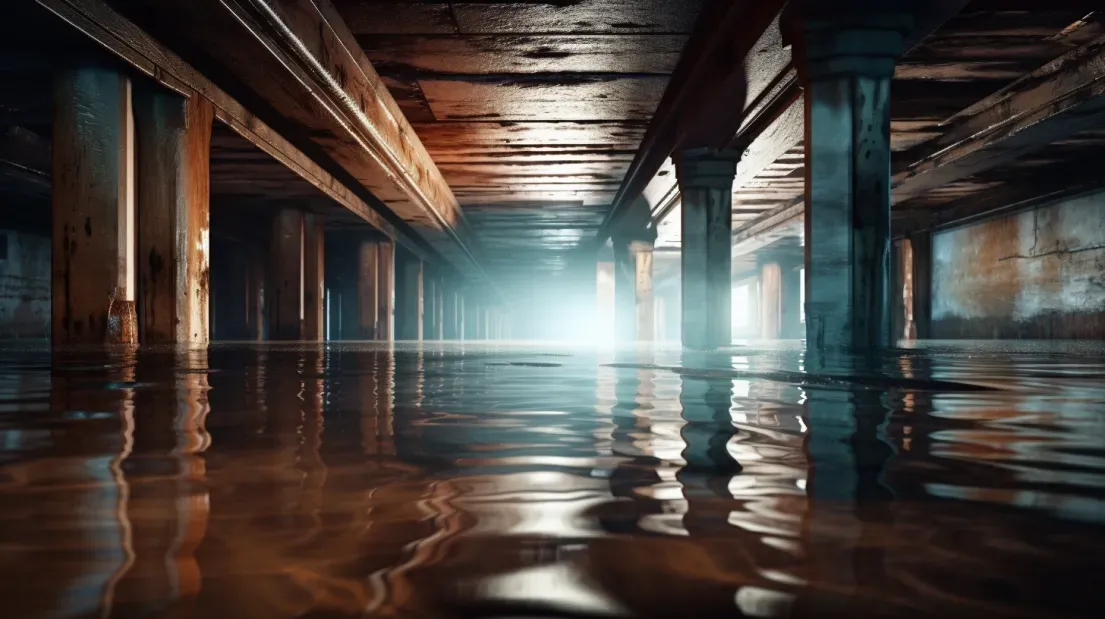
In the realm of construction, ensuring the longevity and durability of buildings is paramount. One critical factor that plays a significant role in achieving this is the effective management of moisture. Moisture barriers, often overlooked, are essential components that prevent water ingress and protect the structural integrity of buildings.
Moisture barriers, also known as vapor barriers or damp-proof membranes, are materials designed to resist the passage of water vapor into walls, floors, and roofs. Their application is crucial in mitigating the adverse effects of moisture, which can lead to a range of problems including mold growth, material decay, and structural damage. These barriers are integral in both residential and commercial construction, ensuring that buildings remain safe, healthy, and durable.
The construction industry employs various types of moisture barriers, each suited to specific conditions and requirements. Common materials used include polyethylene sheets, liquid-applied coatings, and self-adhering membranes. The selection of the appropriate moisture barrier depends on factors such as climate, building design, and the materials used in construction.
In this blog, we will explore the different types of moisture barriers, their applications, and best practices for installation. Understanding these elements is crucial for architects, builders, and homeowners alike, as it equips them with the knowledge to make informed decisions that enhance the resilience and longevity of their constructions. Join us as we delve into the world of moisture barriers, shedding light on their importance and the role they play in modern construction.
Understanding Moisture Barriers
Definition and Purpose
What are moisture barriers?
Moisture barriers, also known as vapor barriers or damp-proof membranes, are materials designed to resist the passage of water vapor into building components such as walls, floors, and roofs. They play a crucial role in the construction industry by preventing moisture from penetrating and accumulating within these structures.
Their role in protecting buildings from moisture damage
Moisture barriers are essential in protecting buildings from the detrimental effects of moisture. Water vapor can enter buildings through diffusion, capillary action, or air movement, leading to various problems such as mold growth, wood rot, corrosion of metal components, and deterioration of insulation. By providing a robust barrier against moisture ingress, these materials help maintain the integrity, safety, and longevity of buildings. They ensure that indoor environments remain healthy and free from moisture-related issues.
Types of Moisture Barriers
Sheet Membranes
Sheet membranes are typically made from materials like polyethylene, rubberized asphalt, or PVC. These membranes are pre-manufactured in large sheets or rolls and are applied to building surfaces during construction. They provide a continuous, impermeable barrier that effectively blocks water vapor. Sheet membranes are often used in below-grade applications, such as foundation walls and slabs, to prevent ground moisture from entering the structure.
Liquid-Applied Membranes
Liquid-applied membranes are coatings that are applied in liquid form and then cured to form a seamless, flexible barrier. These membranes can be sprayed, rolled, or brushed onto surfaces, conforming to complex shapes and details. Once cured, they create a durable, monolithic layer that resists water penetration. Liquid-applied membranes are ideal for roofs, balconies, and areas with irregular geometries where sheet membranes may be challenging to install.
Self-Adhered Membranes
Self-adhered membranes are pre-manufactured sheets with a sticky backing that adheres directly to the substrate without the need for additional adhesives. These membranes are easy to install and provide a consistent thickness, ensuring reliable moisture protection. Self-adhered membranes are commonly used in roofing applications, around windows, doors, and other penetrations where a secure, watertight seal is critical.
Initial Costs of Moisture Barrier Installation
Material Costs
Comparing costs of different types of moisture barriers
The initial cost of moisture barrier installation significantly depends on the type of material chosen. Sheet membranes, typically made from polyethylene or rubberized asphalt, are often more affordable per square foot compared to liquid-applied membranes, which might offer superior flexibility and durability but at a higher price. Self-adhered membranes strike a balance between cost and ease of installation, often priced in the mid-range but providing significant labor cost savings due to their ease of application.
Quality versus price considerations
When selecting a moisture barrier, it's crucial to consider not just the upfront material costs but also the long-term benefits of quality. Higher-priced options often provide better performance, durability, and lifespan, reducing the need for frequent replacements and repairs. Investing in a high-quality moisture barrier can result in overall cost savings by preventing costly moisture damage and maintenance over time.
Labor Costs
Professional installation versus DIY
Labor costs are another major component of the total installation expense. Professional installation ensures that the moisture barrier is applied correctly, maximizing its effectiveness. While this adds to the initial costs, it can prevent improper installation that might lead to future problems. DIY installation can reduce labor costs significantly, but it requires a thorough understanding of the materials and methods to avoid costly mistakes.
Factors influencing labor costs
Several factors influence labor costs, including the complexity of the installation area, the type of moisture barrier used, and local labor rates. Areas with numerous penetrations or irregular shapes may require more time and expertise, increasing labor costs. Additionally, liquid-applied membranes may demand more skill and time compared to sheet or self-adhered membranes, impacting the overall labor expenses.
Equipment and Tools
Necessary tools and their costs
The installation of moisture barriers requires specific tools, which can vary depending on the type of barrier used. For sheet membranes, tools such as utility knives, rollers, and adhesive applicators are essential. Liquid-applied membranes might require spray equipment, brushes, or rollers. Self-adhered membranes typically need simple hand tools but also benefit from the use of rollers to ensure proper adhesion.
Rental versus purchase decisions
Deciding whether to rent or purchase tools depends on the scale and frequency of the projects. For one-time or infrequent installations, renting tools can be more cost-effective, eliminating the need for significant upfront investment. However, for ongoing projects or professional use, purchasing tools might be more economical in the long run, ensuring availability and potentially reducing overall costs over time.
Long-term Financial Benefits
Preventing Moisture Damage
Cost savings from avoiding water damage repairs
Investing in moisture barriers can lead to significant cost savings by preventing water damage. Water intrusion can cause severe damage to building materials, leading to expensive repairs. By installing effective moisture barriers, you can avoid issues such as mold growth, wood rot, and corrosion of metal components. This proactive approach reduces the need for frequent and costly repairs, resulting in substantial long-term savings.
Impact on structural integrity and longevity
Moisture barriers play a crucial role in maintaining the structural integrity of buildings. Water damage can weaken structural elements, compromising the safety and stability of the building. By preventing moisture infiltration, these barriers help preserve the strength and durability of construction materials, enhancing the overall longevity of the building. This long-term benefit ensures that the structure remains safe and sound for many years, reducing the need for major renovations or rebuilds.
Energy Efficiency
Improved insulation and reduced energy costs
Moisture barriers contribute to improved energy efficiency by enhancing the performance of insulation. Moisture can degrade insulation materials, reducing their effectiveness and leading to higher energy consumption for heating and cooling. By keeping insulation dry and intact, moisture barriers help maintain optimal thermal performance, resulting in lower energy costs. This efficiency not only reduces utility bills but also contributes to a more sustainable and environmentally friendly building.
Benefits in different climates and seasons
The benefits of moisture barriers extend across various climates and seasons. In humid climates, they prevent excess moisture from entering the building, reducing the load on air conditioning systems. In colder climates, they prevent condensation and frost buildup within walls, improving heating efficiency. Throughout the year, moisture barriers help maintain a stable indoor environment, enhancing comfort and reducing energy consumption regardless of external weather conditions.
Maintenance and Repairs
Reduced maintenance costs over time
Moisture barriers reduce the need for ongoing maintenance by protecting building components from water damage. Without moisture barriers, frequent inspections and repairs may be necessary to address issues caused by water infiltration. By providing a robust defense against moisture, these barriers help minimize maintenance requirements, resulting in lower long-term costs for building upkeep.
Longevity of moisture barriers and replacement cycles
High-quality moisture barriers are designed to last for many years, providing long-term protection with minimal need for replacement. The longevity of these barriers depends on the materials used and the conditions they are exposed to, but many can last for decades with proper installation. This extended lifespan reduces the frequency of replacement cycles, contributing to cost savings and ensuring continuous protection for the building.
Cost Comparisons
Traditional Construction Methods
Costs without moisture barriers
In traditional construction methods, where moisture barriers are not employed, the initial costs might appear lower. These methods typically rely on conventional building materials and techniques that do not incorporate specialized moisture control measures. However, the absence of moisture barriers can lead to increased susceptibility to water damage, resulting in significant repair and maintenance costs over time.
Long-term financial impact of potential damage
Buildings without moisture barriers are at a higher risk of experiencing moisture-related issues such as mold growth, structural damage, and insulation deterioration. These problems can incur substantial costs, including repairs, replacements, and potential health-related expenses due to mold exposure. Over the long term, the financial impact of not using moisture barriers can far exceed the initial savings, making it a less economical choice for building construction and maintenance.
Alternative Moisture Protection Solutions
Comparison with other moisture management methods
Alternative moisture management solutions, such as drainage systems, sealants, and ventilation improvements, can also be used to control moisture. These methods vary in effectiveness, cost, and complexity. For instance, drainage systems help redirect water away from buildings but might require significant excavation and installation work. Sealants can provide temporary moisture protection but may need regular reapplication. Ventilation improvements can reduce indoor humidity but do not address moisture penetration from external sources.
Cost-benefit analysis of each approach
When comparing moisture barriers to other moisture management solutions, it's essential to conduct a thorough cost-benefit analysis. Moisture barriers, while potentially more expensive initially, offer long-lasting and reliable protection that minimizes maintenance needs and prevents costly damage. Drainage systems and sealants might have lower upfront costs but often come with higher maintenance and replacement expenses. Improved ventilation can enhance indoor air quality and reduce humidity but does not provide a physical barrier against water ingress.
Moisture barriers present a comprehensive solution with a favorable cost-benefit ratio, as their ability to prevent moisture intrusion helps maintain the structural integrity and longevity of buildings. Investing in high-quality moisture barriers can lead to overall cost savings by reducing the need for frequent repairs and enhancing the building's resilience against moisture-related issues.
Factors Influencing Cost-Effectiveness
Building Type and Location
Residential versus commercial buildings
The cost-effectiveness of moisture barriers can vary significantly between residential and commercial buildings. Residential buildings generally have smaller footprints and simpler designs, which can make the installation of moisture barriers more straightforward and cost-effective. In contrast, commercial buildings often have larger areas and more complex structures, potentially increasing the costs associated with moisture barrier installation. However, the higher initial investment in commercial buildings can lead to substantial long-term savings by protecting valuable assets and preventing business interruptions due to moisture damage.
Climate and environmental considerations
The effectiveness and necessity of moisture barriers are heavily influenced by the climate and environmental conditions of the building location. In areas with high humidity or frequent rainfall, the need for robust moisture protection is greater, making the investment in quality moisture barriers more cost-effective. Conversely, in arid climates, the risk of moisture damage is lower, but it is still essential to consider potential issues such as groundwater or condensation. Tailoring the moisture barrier solution to the specific environmental conditions ensures optimal performance and cost-efficiency.
Installation Quality
Impact of professional installation on effectiveness
The quality of installation plays a critical role in the effectiveness of moisture barriers. Professional installation ensures that the barriers are applied correctly, minimizing the risk of gaps, overlaps, or other installation errors that can compromise their performance. Proper installation is especially important for complex areas such as corners, joints, and penetrations. While professional installation might increase initial costs, it significantly enhances the barrier's reliability and longevity, providing better overall value.
Common pitfalls and how to avoid them
Common pitfalls in moisture barrier installation include improper surface preparation, incorrect application techniques, and the use of substandard materials. These issues can lead to premature failure of the barrier, resulting in increased maintenance and repair costs. To avoid these pitfalls, it is crucial to follow manufacturer guidelines, employ skilled installers, and conduct thorough inspections during and after installation. Ensuring that the installation is done correctly from the outset can prevent costly problems down the line.
Material Durability
Longevity and performance of different materials
The durability of moisture barrier materials is a key factor in their cost-effectiveness. High-quality materials, such as rubberized asphalt or advanced polymers, typically offer superior performance and longer lifespans compared to cheaper alternatives. While these materials may have higher upfront costs, their extended durability reduces the frequency of replacement and maintenance, leading to lower long-term expenses.
Balancing initial costs with long-term benefits
Balancing initial costs with long-term benefits involves considering the total cost of ownership rather than just the upfront expenditure. Investing in durable, high-performance moisture barriers may seem costly initially, but the long-term benefits, including reduced repair costs, extended building lifespan, and enhanced property value, can outweigh these initial expenses. Evaluating the cost-effectiveness of moisture barriers requires a comprehensive analysis of their performance, durability, and the specific needs of the building project.
FAQs
Contact Bull City Crawlspace Today!
Bull City Crawlspace will do everything we can to ensure your experience with us is excellent.
Request A FREE Estimate
Request a Free Estimate Form
Checkout Recent Post
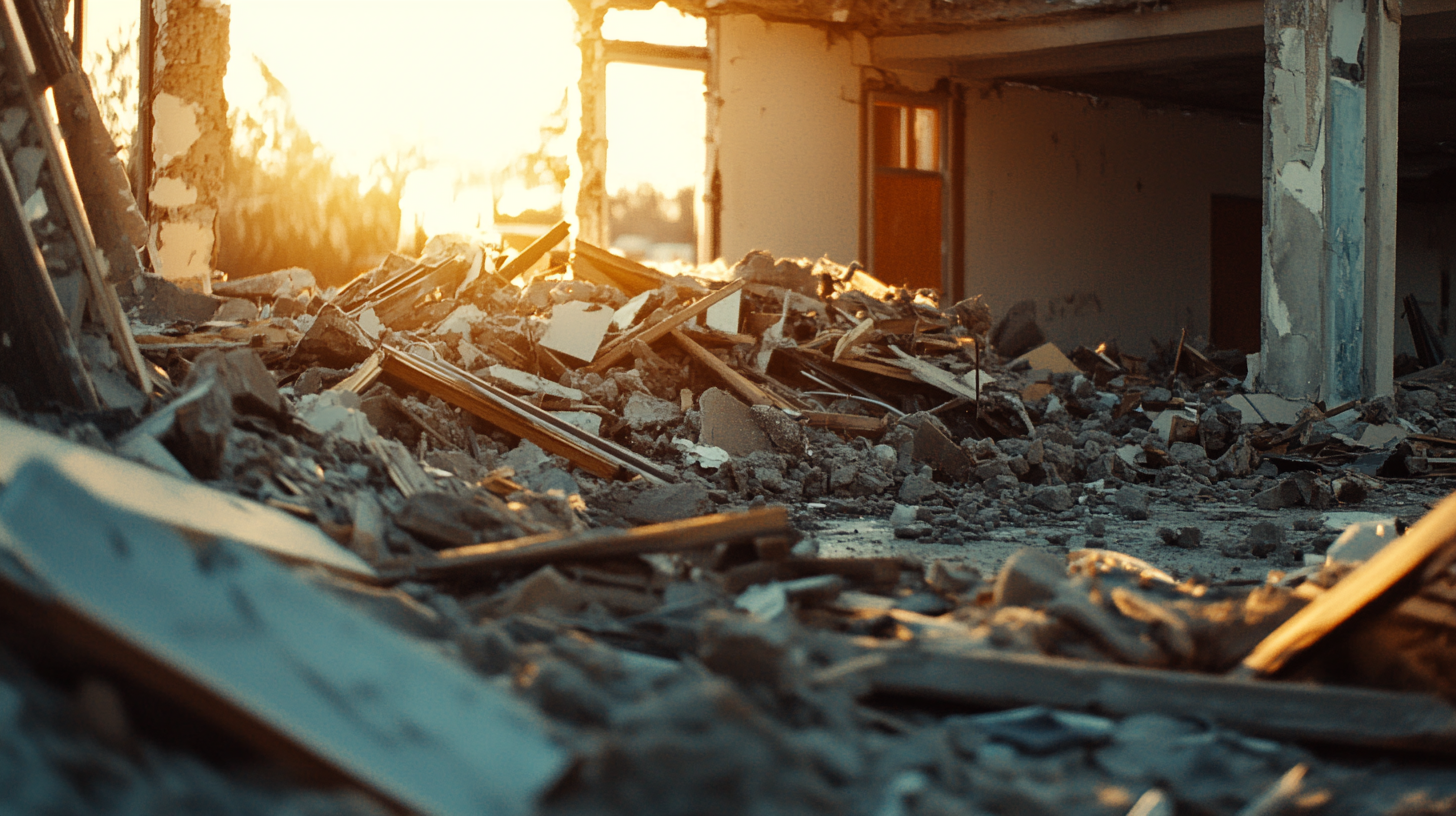
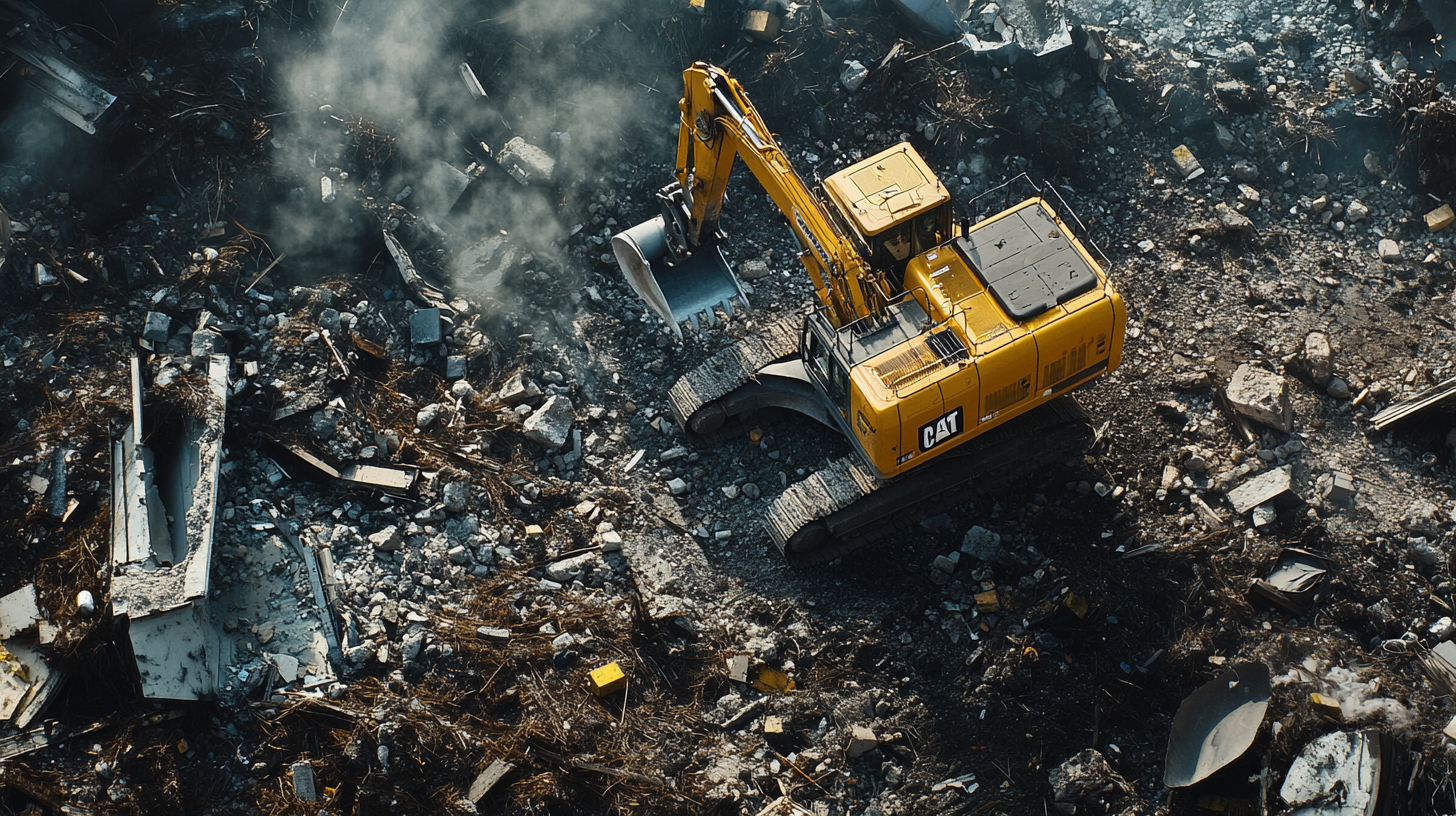


Got a Question? We’re Here to Help.
You can arrange an appointment or make an enquiry by phone or email, orget in touch to us via our contact form.