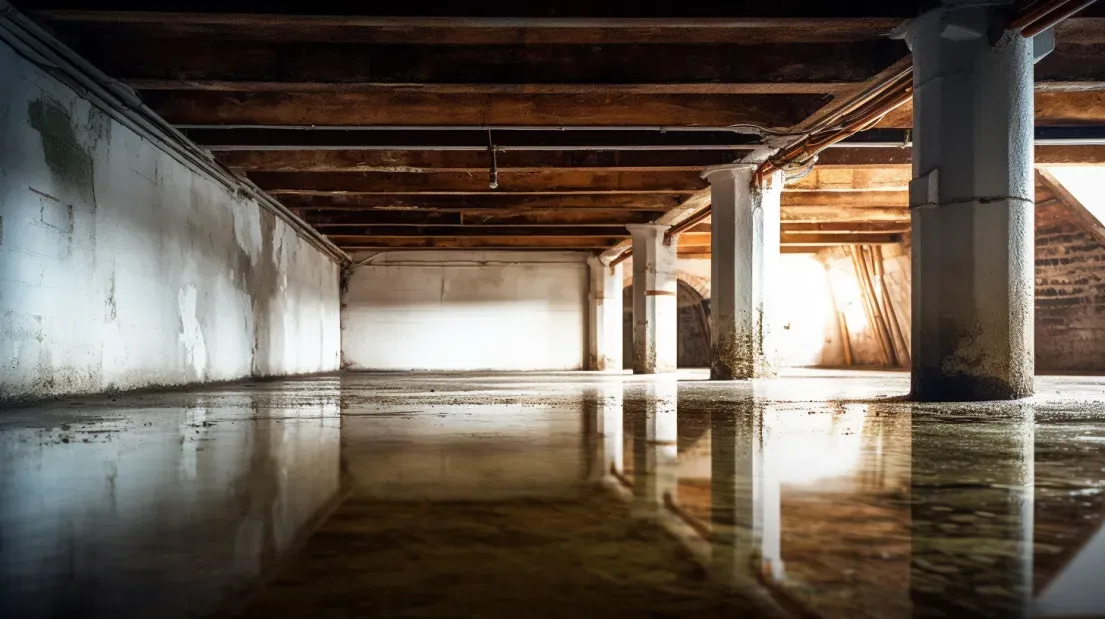
In the field of construction, ensuring the durability and longevity of buildings is of paramount importance. One critical aspect that significantly contributes to this goal is the effective management of moisture. Moisture barriers, often known as vapor barriers or damp-proof membranes, are essential components in modern construction practices. These barriers are designed to prevent water vapor from penetrating building materials, thereby safeguarding the structural integrity and interior environments of buildings.
Moisture barriers play a crucial role in protecting buildings from a wide array of moisture-related issues. Without proper moisture control, buildings are susceptible to problems such as mold growth, wood rot, corrosion of metal components, and deterioration of insulation. These issues not only compromise the structural strength of buildings but also pose health risks to occupants and lead to increased maintenance and repair costs.
The application of moisture barriers is essential in both residential and commercial construction, providing a first line of defense against moisture intrusion. By effectively blocking water vapor, these barriers help maintain a dry and stable indoor environment, which is vital for the comfort and well-being of occupants. Additionally, moisture barriers contribute to improved energy efficiency by ensuring that insulation remains dry and effective, thereby reducing heating and cooling costs.
In this blog, we will explore the various types of moisture barriers available, their specific applications, and the long-term financial benefits they offer. Understanding the importance of moisture barriers in construction is crucial for architects, builders, and homeowners alike, as it equips them with the knowledge to make informed decisions that enhance the durability and efficiency of their buildings. Join us as we delve into the world of moisture barriers, highlighting their significance and the critical role they play in contemporary construction practices.
Residential Construction
Common Moisture Issues
Typical moisture problems in residential buildings
Residential buildings frequently encounter moisture problems that can lead to significant damage and health concerns. Common issues include water infiltration through foundations, walls, and roofs, condensation buildup in poorly ventilated areas, and leaks from plumbing systems. These moisture problems can cause mold growth, wood rot, and deterioration of building materials, compromising the structural integrity and indoor air quality of homes.
Impact of moisture on residential structures
Moisture can have a profound impact on residential structures. Persistent dampness can weaken wooden frames, leading to structural instability. It can also cause metal components to corrode, reducing their load-bearing capacity. Furthermore, moisture-related problems can degrade insulation, reducing its effectiveness and leading to increased energy costs. The presence of mold and mildew can also pose serious health risks to occupants, contributing to respiratory issues and allergic reactions.
Best Practices for Residential Moisture Barriers
Selecting appropriate moisture barriers
Choosing the right moisture barrier for residential construction involves considering factors such as the local climate, the specific areas of the home prone to moisture exposure, and the types of building materials used. Options include sheet membranes, liquid-applied membranes, and self-adhered membranes, each offering different levels of protection and suitability for various applications. It is essential to select a moisture barrier that provides reliable protection while being compatible with the building's design and materials.
Installation techniques for residential settings
Proper installation of moisture barriers is crucial to ensure their effectiveness. In residential settings, this involves meticulous preparation of surfaces, ensuring they are clean, dry, and free from defects. Installation techniques vary depending on the type of barrier used; for instance, sheet membranes require precise cutting and sealing at seams and edges, while liquid-applied membranes must be evenly applied to achieve a uniform thickness. Attention to detail during installation helps prevent gaps or overlaps that could compromise the barrier's performance.
Case study: Successful residential moisture barrier installation
Consider a case study of a successful residential moisture barrier installation in a humid climate. A homeowner in Florida experienced frequent moisture problems, including mold growth and wood rot, due to high humidity and occasional flooding. By consulting with a professional contractor, the homeowner selected a combination of sheet membranes for the foundation and liquid-applied membranes for the walls and roof. The installation was meticulously carried out, with particular attention to sealing joints and penetrations. As a result, the home remained dry and free from moisture-related issues, significantly improving indoor air quality and reducing maintenance costs. This case study highlights the importance of selecting appropriate moisture barriers and ensuring their proper installation to protect residential structures effectively.
Historical and Renovation Projects
Moisture Concerns in Historical Buildings
Common moisture problems in older structures
Historical buildings often face significant moisture challenges due to their age and the construction methods used at the time. Common problems include rising damp, where moisture from the ground moves up through the walls; penetrating damp, where water enters the building through external walls; and condensation issues caused by inadequate ventilation. These moisture problems can lead to severe deterioration of building materials, especially in structures that have not been updated with modern moisture control measures.
Impact of moisture on historical buildings
The impact of moisture on historical buildings is profound. Water ingress can cause decay in wooden beams and flooring, corrosion of metal fixtures, and crumbling of masonry and plaster. This not only threatens the structural integrity of the building but also damages historically significant features and finishes. Preserving the architectural and cultural heritage of these buildings requires effective moisture management strategies to prevent ongoing damage and maintain their historical value.
Handling Moisture Barriers in Renovation Projects
Selecting appropriate barriers for renovations
Selecting appropriate moisture barriers for renovation projects involves considering the specific needs of the historical building and the types of moisture problems it faces. It is essential to choose materials that are compatible with the original construction methods and materials to avoid adverse reactions. For instance, breathable membranes may be preferred to allow any trapped moisture within the walls to escape, preventing further damage. Additionally, the barriers must be discreet and non-invasive to preserve the building's historical appearance.
Techniques for installing barriers in historical buildings
Installing moisture barriers in historical buildings requires careful planning and execution to ensure minimal disruption to the original structure. Techniques may include the application of liquid-applied membranes that can conform to irregular surfaces, the use of sheet membranes in areas that can accommodate them without altering the building's aesthetics, and ensuring that all installations are reversible where possible. Proper installation also involves sealing all joints and penetrations effectively to prevent moisture ingress while maintaining the building's historical integrity.
Case study: Moisture barrier application in a renovation project
A notable case study involves the renovation of a 19th-century Victorian townhouse. The building suffered from rising damp and penetrating damp, which had caused significant damage to the wooden floors and internal plasterwork. During the renovation, a combination of breathable sheet membranes and liquid-applied membranes were used. The sheet membranes were installed on the ground floors to prevent rising damp, while liquid-applied membranes were used on the external walls to combat penetrating damp. The installation was done with great care to preserve the original woodwork and decorative elements. As a result, the townhouse was effectively protected from moisture, and the historical features were preserved, demonstrating the effectiveness of carefully selected and installed moisture barriers in renovation projects.
Commercial Construction
Challenges in Commercial Buildings
Unique moisture challenges in commercial construction
Commercial buildings face unique moisture challenges due to their size, design complexity, and the variety of activities they host. Large roof areas, extensive basements, and complex HVAC systems can create numerous pathways for moisture infiltration. Additionally, the presence of high-traffic areas, food service operations, and extensive plumbing networks increases the risk of moisture problems. Commercial buildings often have varied occupancy patterns and uses, leading to fluctuating humidity levels that further complicate moisture control.
Examples of moisture problems in commercial buildings
Examples of moisture problems in commercial buildings include leaks from roofs and windows, condensation in HVAC systems, and water damage from plumbing failures. For instance, a large office building might experience condensation issues due to inadequate ventilation, leading to mold growth in ceiling tiles and ductwork. Shopping centers with extensive flat roofs are prone to leaks, causing damage to retail spaces and merchandise. Warehouses with poor drainage can suffer from groundwater seepage, leading to structural damage and compromised inventory.
Effective Strategies for Commercial Moisture Barriers
Choosing the right materials for commercial projects
Selecting the appropriate moisture barrier materials for commercial projects involves considering the building’s specific needs and environmental conditions. For example, high-traffic areas and heavy equipment usage in commercial buildings require durable materials like rubberized asphalt or reinforced polyethylene sheets. These materials provide robust protection against water infiltration and withstand the physical demands of a commercial environment. In areas with high humidity or frequent rainfall, materials with high permeability ratings are essential to allow trapped moisture to escape, preventing mold and mildew growth.
Installation methods suited for commercial environments
Installation methods for moisture barriers in commercial settings must account for the scale and complexity of these buildings. Techniques such as liquid-applied membranes are beneficial for irregular surfaces and large areas, providing a seamless barrier that conforms to various shapes and penetrations. Sheet membranes, when used, should be meticulously sealed at seams and around penetrations to ensure complete coverage. Professional installation is crucial in commercial projects to address the complex needs and ensure the long-term effectiveness of the moisture barriers.
Case study: Commercial building moisture barrier solutions
Consider a case study of a multi-story commercial office building that experienced significant moisture problems due to a leaking roof and poor drainage. The building’s management decided to install a combination of sheet and liquid-applied membranes to address these issues. The roof was covered with a high-performance sheet membrane, while liquid-applied membranes were used in the basement and around windows. This comprehensive approach effectively prevented water ingress, reducing repair costs and improving the building’s overall resilience. The case study demonstrates how selecting the right materials and installation techniques can successfully mitigate moisture problems in commercial buildings.
Industrial Construction
Moisture Risks in Industrial Settings
Specific moisture issues in industrial buildings
Industrial buildings are exposed to unique moisture risks due to the nature of their operations and the materials they house. Common moisture issues include condensation from high-temperature processes, leaks from extensive plumbing systems, and water ingress through large roof surfaces. The use of heavy machinery and chemicals can exacerbate these problems by creating environments with varying humidity and temperature levels. Additionally, industrial buildings often have large, open spaces that make it challenging to control moisture effectively.
Consequences of moisture problems in industrial environments
Moisture problems in industrial settings can lead to severe consequences, including corrosion of metal structures and machinery, degradation of stored materials, and the growth of mold and mildew, which can impact air quality and worker health. Persistent moisture issues can also compromise the integrity of the building, leading to costly repairs and potential safety hazards. For instance, electrical systems can short-circuit due to water ingress, posing significant fire risks. Addressing these moisture issues is crucial to maintaining operational efficiency and safety in industrial environments.
Implementing Moisture Barriers in Industrial Construction
Material selection for industrial applications
Selecting the right materials for moisture barriers in industrial buildings is critical to ensure durability and effectiveness. Materials must withstand harsh conditions, such as chemical exposure and extreme temperatures. High-performance membranes, such as reinforced polyethylene, rubberized asphalt, and liquid-applied polymers, are ideal for these environments. These materials offer robust protection against moisture while being resistant to industrial chemicals and physical wear. Choosing materials with high tensile strength and flexibility ensures they can accommodate the movements and stresses typical in industrial settings.
Techniques for effective barrier installation in industrial buildings
Effective installation of moisture barriers in industrial buildings involves meticulous planning and execution to address the unique challenges of these environments. Techniques include applying liquid-applied membranes to complex and irregular surfaces, ensuring complete coverage and sealing around all penetrations and joints. For large, flat areas like roofs, sheet membranes with reinforced seams provide robust protection. It is essential to ensure that all barriers are applied according to manufacturer specifications and industry best practices to maximize their performance. Regular inspections and maintenance are also vital to address any wear or damage promptly.
Case study: Industrial moisture barrier project
A case study example involves a manufacturing facility that faced significant moisture issues due to its high-temperature operations and extensive use of water in production processes. The facility management decided to implement a comprehensive moisture barrier system using a combination of liquid-applied and sheet membranes. The liquid-applied membranes were used in areas with complex equipment layouts, ensuring seamless protection, while reinforced sheet membranes were installed on large roof sections. The installation was carried out by specialized contractors who ensured all penetrations and joints were meticulously sealed. As a result, the facility experienced a significant reduction in moisture-related problems, leading to improved operational efficiency and reduced maintenance costs. This case study demonstrates the importance of selecting the right materials and installation techniques for effective moisture control in industrial settings.
High-Rise Construction
High-Rise Moisture Challenges
Special considerations for moisture control in high-rises
High-rise buildings present unique challenges for moisture control due to their height, exposure to varying weather conditions, and complex structural designs. The significant height of these structures means they are more susceptible to wind-driven rain and air pressure differences, which can drive moisture into the building envelope. Additionally, the sheer scale of high-rises requires careful planning to ensure moisture barriers are continuous and effective across all floors and interfaces. Special considerations include the need for durable materials that can withstand high wind loads and the use of advanced sealing techniques to prevent moisture ingress at joints and penetrations.
Examples of moisture issues in tall buildings
Moisture issues in tall buildings can manifest in various ways, including water infiltration through the building envelope, condensation within wall cavities, and leaks from roofs and terraces. For instance, improper sealing of windows and curtain walls can lead to water penetration, causing damage to interior finishes and promoting mold growth. High-rise buildings also often have extensive mechanical systems, where condensation can occur if proper insulation and vapor barriers are not installed, leading to corrosion and system failures.
Moisture Barrier Solutions for High-Rise Buildings
Best materials for high-rise construction
Selecting the best materials for moisture barriers in high-rise construction is crucial for long-term performance and durability. High-performance materials such as ethylene propylene diene monomer (EPDM) membranes, thermoplastic polyolefin (TPO) membranes, and liquid-applied polyurethane coatings are commonly used. These materials offer excellent resistance to UV radiation, extreme temperatures, and mechanical stress. Additionally, they provide flexibility to accommodate building movements and are robust enough to handle the unique demands of high-rise environments.
Advanced installation techniques for high-rise structures
Advanced installation techniques are essential to ensure the effectiveness of moisture barriers in high-rise buildings. Techniques include the use of continuous air barriers that integrate with the moisture barrier system, detailed sealing of all joints and penetrations, and the application of liquid membranes to cover complex geometries and ensure seamless protection. High-rise construction often involves prefabricated elements, so ensuring proper sealing during assembly is critical. Additionally, implementing redundant barrier systems can provide extra protection against moisture ingress, enhancing the overall resilience of the building envelope.
Case study: Moisture barrier installation in a high-rise project
A notable case study involves the installation of moisture barriers in a new 50-story office tower located in a coastal city prone to high winds and heavy rainfall. The project faced significant challenges due to the building's height and exposure to harsh weather conditions. The construction team selected a combination of EPDM and liquid-applied polyurethane membranes for the building envelope. These materials were chosen for their durability and flexibility. The installation process included meticulous sealing of all windows, curtain walls, and roof edges using advanced sealing tapes and liquid membranes to ensure continuous protection. Regular inspections and quality control checks were conducted throughout the installation to ensure adherence to best practices. As a result, the building has remained free from moisture issues, demonstrating the effectiveness of well-chosen materials and advanced installation techniques in high-rise construction.
FAQs
Contact Bull City Crawlspace Today!
Bull City Crawlspace will do everything we can to ensure your experience with us is excellent.
Request A FREE Estimate
Request a Free Estimate Form
Checkout Recent Post
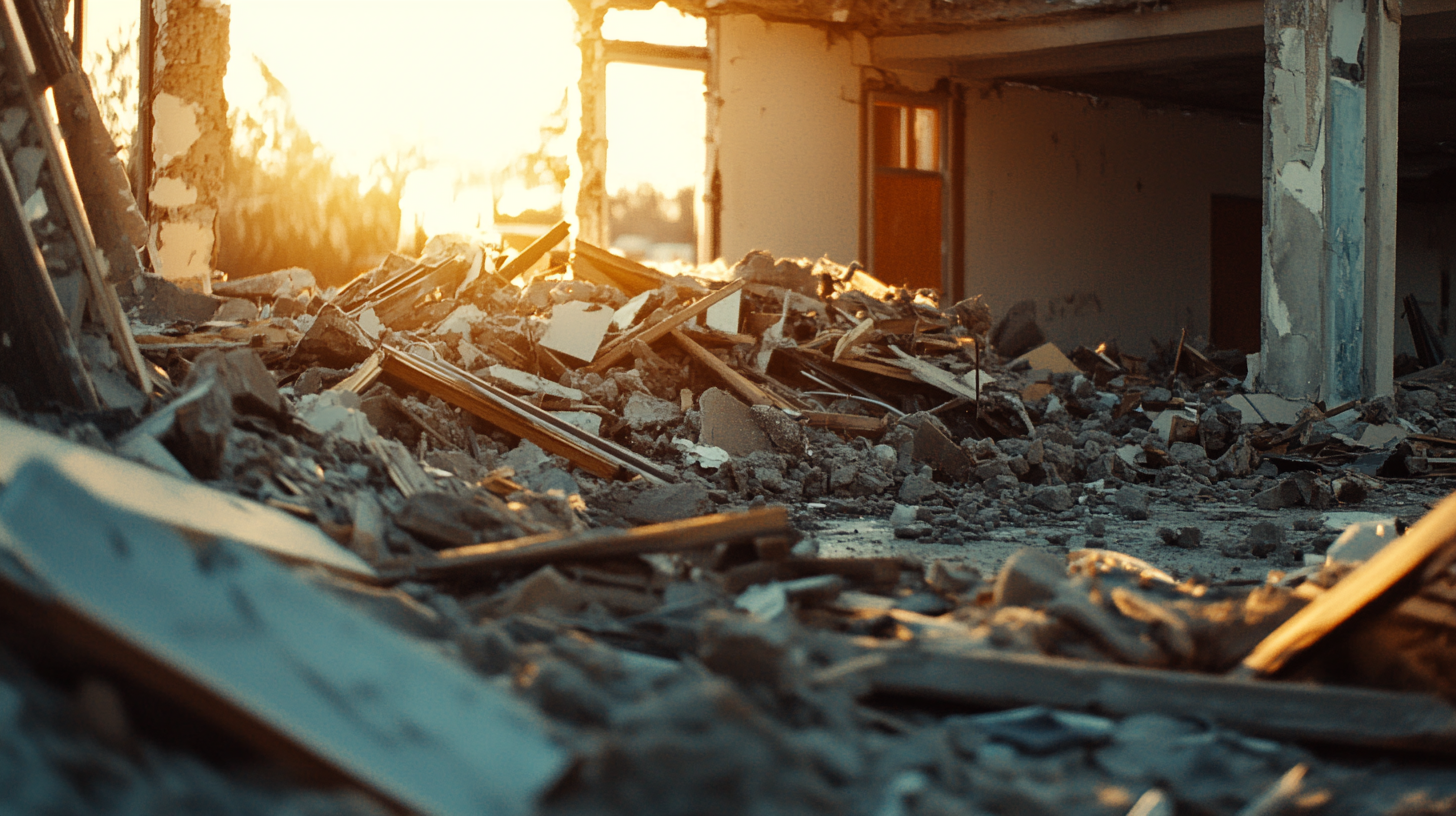
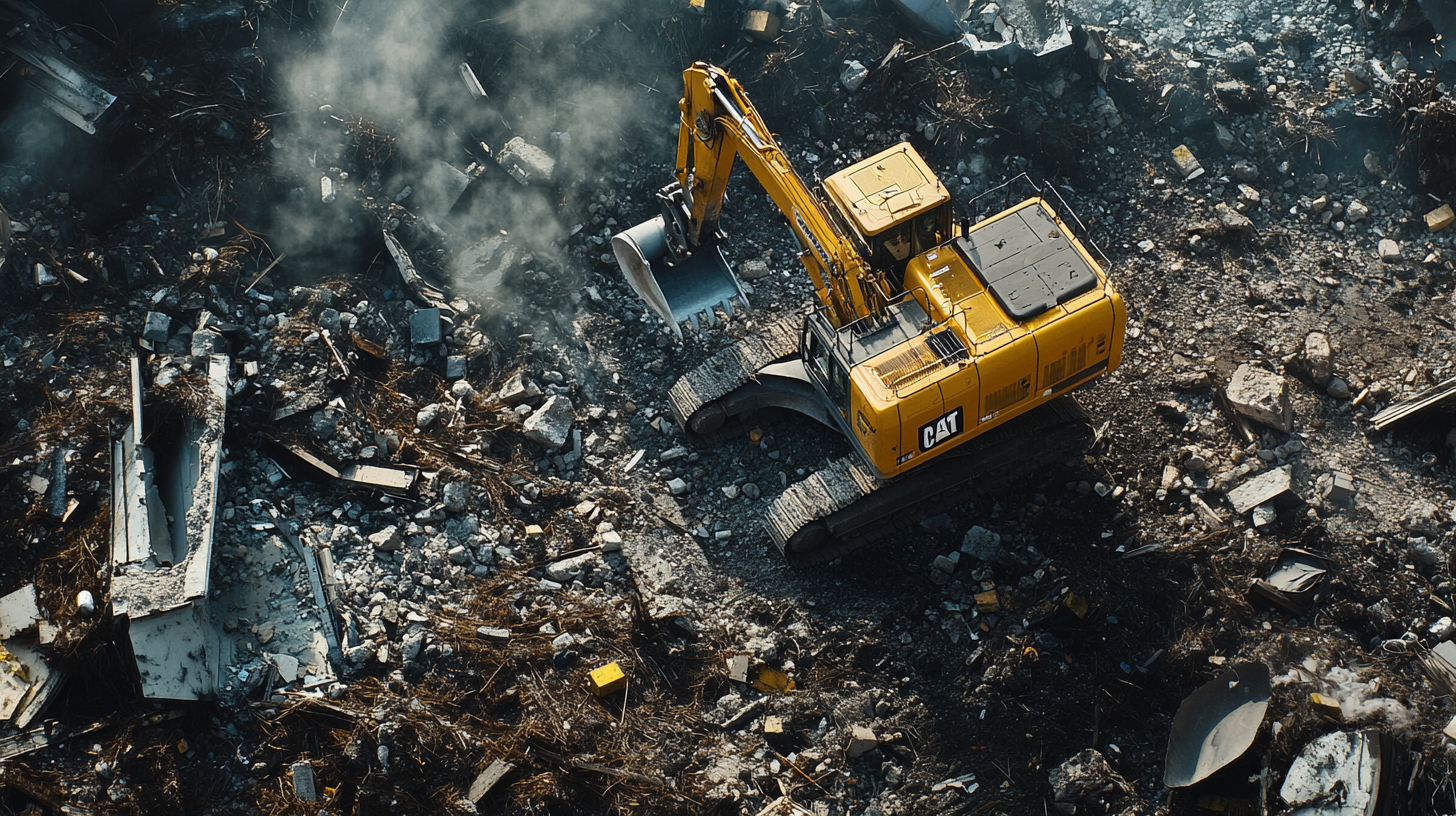


Got a Question? We’re Here to Help.
You can arrange an appointment or make an enquiry by phone or email, orget in touch to us via our contact form.