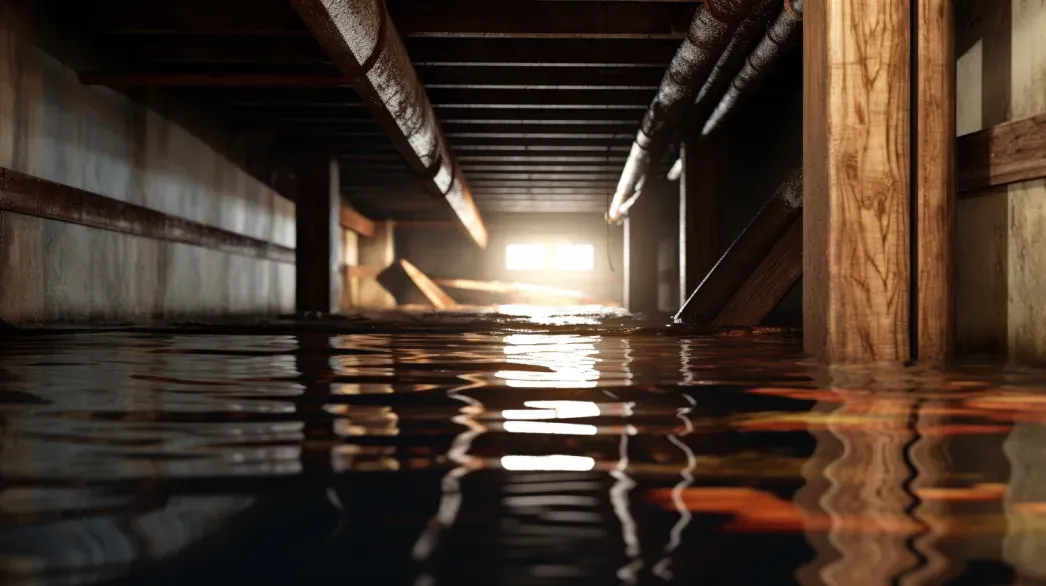
Concrete floors are a popular choice in both residential and commercial construction due to their durability, versatility, and cost-effectiveness. However, one critical aspect that often gets overlooked is the need for proper moisture management. Moisture barriers play an essential role in protecting concrete floors from potential damage caused by water and vapor infiltration. This blog aims to highlight the importance of moisture barriers for concrete floors, explaining how they function, their benefits, and the consequences of neglecting this crucial component in your flooring system.
What Are Moisture Barriers?
Moisture barriers, also known as vapor barriers, are materials designed to prevent the passage of moisture from the ground into the concrete slab. These barriers are typically installed beneath the concrete floor during the construction phase. They can be made from various materials, including polyethylene sheets, liquid-applied membranes, or other synthetic materials, each with different levels of effectiveness depending on the specific application and environmental conditions.
How Moisture Barriers Work
The primary function of a moisture barrier is to act as a protective layer that prevents water vapor from rising through the concrete slab. This is particularly important in areas with high groundwater levels or where the soil retains significant moisture. By blocking moisture migration, these barriers help maintain the structural integrity of the concrete, prevent the growth of mold and mildew, and protect the flooring materials and finishes applied over the concrete.
Benefits of Moisture Barriers
Enhanced Durability: Moisture barriers extend the life of concrete floors by preventing water-related damage such as cracking, spalling, and weakening of the slab.
Mold and Mildew Prevention: By keeping moisture at bay, these barriers reduce the risk of mold and mildew growth, which can lead to health issues and unpleasant odors.
Protection of Flooring Materials: Flooring materials such as wood, vinyl, and carpets are susceptible to damage from moisture. A moisture barrier ensures these materials remain dry and intact.
- Energy Efficiency: Moisture barriers can contribute to better insulation, helping to regulate indoor temperatures and reduce energy costs.
- Cost Savings: Investing in a moisture barrier can save money in the long run by avoiding costly repairs and replacements due to moisture damage.
Consequences of Skipping Moisture Barriers
Neglecting to install a moisture barrier can lead to several problems:
- Structural Damage: Persistent moisture can compromise the concrete's structural integrity, leading to cracks and weakening over time.
- Health Hazards: The presence of moisture can promote mold growth, posing health risks to occupants.
- Flooring Failures: Without a moisture barrier, floor coverings may warp, buckle, or delaminate, requiring premature replacement.
- Increased Maintenance Costs: Addressing moisture-related issues can be expensive and time-consuming, far outweighing the initial investment in a moisture barrier.
In conclusion, moisture barriers are a vital component in ensuring the longevity and performance of concrete floors. By effectively managing moisture, they protect the structural integrity of the concrete, preserve the quality of flooring materials, and promote a healthier indoor environment. Whether you are constructing a new building or renovating an existing one, incorporating a moisture barrier is a wise investment that will pay off in the long term.
Step 1: Clean and Prepare the Concrete Floor
Proper preparation of a concrete floor is crucial for ensuring the effectiveness and longevity of any subsequent treatments or flooring installations. This initial step involves two key tasks: removing debris and existing flooring materials, and repairing and smoothing the concrete surface. Attention to detail during this phase will help create a solid foundation for further work.
Removing Debris and Existing Flooring
Before any repairs or installations can begin, it's essential to clear the concrete floor of any debris, dust, and remnants of old flooring materials. This process involves the following steps:
- Clearing Out Debris: Begin by removing any large pieces of debris from the surface of the concrete. This can include chunks of old flooring, loose dirt, and other materials that may be scattered across the floor.
- Removing Old Flooring Materials: If there are remnants of old flooring such as carpet, tiles, or vinyl, these need to be carefully removed. Use appropriate tools such as a scraper, chisel, or pry bar to lift and dispose of these materials.
- Cleaning the Surface: Once the larger debris and old flooring materials have been removed, it's time to thoroughly clean the surface. Use a broom to sweep up any remaining dirt and dust. For a more thorough cleaning, a vacuum can be used to ensure that all fine particles are removed. This step is crucial as it ensures that no loose material remains that could interfere with the next stages of preparation.
Repairing and Smoothing the Surface
With the floor clean and free of debris, the next step is to repair any damage to the concrete and ensure that the surface is smooth and level. This process includes:
- Fixing Cracks and Holes: Inspect the concrete floor for any cracks, holes, or other imperfections. These need to be repaired to prevent further deterioration and to create a smooth base for flooring installation. Use a concrete patching compound to fill in these cracks and holes. Follow the manufacturer’s instructions for mixing and applying the compound, ensuring that it is level with the rest of the floor surface.
- Ensuring the Floor is Level and Smooth: After repairing any damage, check the entire surface of the floor to ensure it is level. Use a straight edge or a level to identify any high or low spots. If the floor is uneven, it may be necessary to use a self-leveling compound. Apply the compound according to the instructions, allowing it to flow and settle into a smooth, even surface. This step is vital for preventing issues with the installation of new flooring materials and ensuring a long-lasting finish.
By meticulously cleaning and preparing the concrete floor, you create an ideal foundation for any further work. This step not only ensures that the surface is ready for the application of moisture barriers, coatings, or new flooring materials but also helps to extend the lifespan and performance of the finished floor. Taking the time to thoroughly prepare the concrete will pay off in the long run, resulting in a more durable and aesthetically pleasing outcome.
Step 2: Measure and Cut the Moisture Barrier
Accurate measurement and precise cutting of the moisture barrier are essential steps to ensure the effective protection of concrete floors from moisture infiltration. This process involves two main tasks: measuring the floor area accurately and cutting the moisture barrier to fit perfectly. Following these steps will help create a seamless and efficient moisture barrier installation.
Measuring the Floor Area
The first task in this step is to measure the floor area that needs to be covered by the moisture barrier. Accurate measurements are crucial to avoid wastage and ensure complete coverage. Here’s how to do it:
Accurate Measurement Techniques:
- Gather Tools: Use a measuring tape, notepad, and pencil to record dimensions. A laser measure can also be useful for large or irregular spaces.
- Measure the Length and Width: Start by measuring the length and width of the room. Measure along the baseboards to ensure precision. If the room is not perfectly rectangular, measure each section separately and sum the areas.
- Record Dimensions: Write down all measurements clearly. For irregularly shaped rooms, sketch a simple floor plan and note the dimensions on the sketch.
Allowing Extra Material for Overlaps and Seams:
- Add Extra Material: When calculating the amount of moisture barrier needed, add extra material to allow for overlaps and seams. Typically, an additional 2-3 inches along each edge should suffice to ensure proper coverage and effective moisture blocking.
- Account for Obstacles: Measure around any obstacles such as columns, pipes, or built-in furniture. Include these in your calculations to ensure the barrier fits well around these areas.
Cutting the Barrier
With accurate measurements in hand, the next task is to cut the moisture barrier to fit the floor dimensions precisely. Proper cutting techniques will help ensure a seamless installation:
Using a Utility Knife for Precise Cuts:
- Gather Cutting Tools: Use a sharp utility knife and a straightedge or metal ruler. A cutting mat can protect underlying surfaces and provide a clean cutting area.
- Mark the Measurements: Lay out the moisture barrier on a flat surface. Using the measurements taken earlier, mark the dimensions directly on the barrier with a pencil or marker. Ensure your marks are straight and clear.
Cutting Pieces to Fit the Dimensions of the Floor:
- Make Initial Cuts: Start by making the initial straight cuts along the marked lines. Use the straightedge to guide your utility knife, ensuring clean, straight edges.
- Cut for Overlaps: When cutting pieces for areas that will overlap, add the extra inches you accounted for in your measurements. This ensures that the pieces will overlap correctly when laid down.
- Cut Around Obstacles: For any obstacles identified earlier, measure and cut around these carefully. It may be helpful to cut smaller pieces and fit them around the obstacles to ensure complete coverage without gaps.
By meticulously measuring and cutting the moisture barrier, you ensure that the material fits the floor area perfectly, providing an effective barrier against moisture. Taking the time to measure accurately and cut precisely helps prevent gaps and overlaps that could compromise the barrier’s effectiveness, ultimately protecting the integrity of your concrete floor and any applied flooring materials.
Step 3: Installing the Moisture Barrier
Proper installation of the moisture barrier is critical to ensure its effectiveness in protecting concrete floors from moisture infiltration. This step involves laying out the barrier, securing it, and optionally applying a liquid-applied barrier for added protection. Following these detailed instructions will help achieve a seamless and efficient installation.
Laying Out the Barrier
The first task is to lay out the moisture barrier across the floor. This process involves careful handling and placement of the polyethylene sheeting to ensure complete and smooth coverage:
Rolling Out Polyethylene Sheeting Across the Floor:
- Position the Roll: Start at one end of the room and position the roll of polyethylene sheeting. Unroll the material slowly, covering the entire floor area.
- Overlap the Edges: Ensure that each new section of sheeting overlaps the previous one by 2-3 inches. This overlap is crucial for preventing gaps where moisture could seep through.
Ensuring the Barrier Lays Flat Without Wrinkles or Bubbles:
- Smooth the Sheeting: As you unroll the sheeting, use your hands or a broom to smooth it out, removing any wrinkles or bubbles. Ensuring the barrier lies flat will enhance its effectiveness and prevent any disruptions to the flooring installed on top.
- Adjust as Necessary: If you encounter any obstacles or irregularities, carefully cut and fit the sheeting around these areas, ensuring a snug fit without any gaps.
Securing the Floor Barrier
Once the barrier is laid out flat and overlaps are in place, the next step is to secure the barrier. This ensures it remains in position and provides a continuous moisture seal:
Using Adhesive Tape to Secure Seams and Overlaps:
- Tape the Seams: Use a high-quality adhesive tape designed for polyethylene sheeting. Apply the tape along the seams where sections of the barrier overlap. Press down firmly to ensure a tight bond.
- Check the Edges: Double-check that all seams and overlaps are securely taped, with no gaps or loose edges.
Ensuring a Tight Seal with the Wall Barriers (if applicable):
Seal to the Walls: If your installation requires the moisture barrier to extend up the walls, use the adhesive tape to secure the barrier to the walls. Ensure a tight seal where the floor barrier meets the wall barriers to prevent any moisture from bypassing the barrier at these junctions.
Applying Liquid-Applied Barriers (Optional)
For added protection, you may choose to apply a liquid-applied moisture barrier. This step is optional but can provide an extra layer of defense against moisture infiltration:
Using a Trowel to Spread the Liquid Barrier Evenly:
- Prepare the Liquid Barrier: Follow the manufacturer’s instructions to prepare the liquid barrier. Pour a manageable amount onto the floor.
- Spread with a Trowel: Use a trowel to spread the liquid barrier evenly across the surface of the concrete. Work in small sections to ensure uniform coverage and avoid pooling.
Allowing Sufficient Drying Time as per Manufacturer Instructions:
- Drying Time: Allow the liquid-applied barrier to dry thoroughly as per the manufacturer’s instructions. This may take several hours to a day, depending on the product and environmental conditions.
- Check for Completeness: Once dried, inspect the surface to ensure the barrier has formed a consistent and continuous layer without any missed spots.
By following these steps meticulously, you ensure that the moisture barrier is effectively installed, providing robust protection against moisture infiltration. This will help preserve the integrity of the concrete floor and any flooring materials applied on top, ensuring a long-lasting and durable flooring system.
Step 4: Sealing the Edges and Seams
The final step in installing a moisture barrier for concrete floors involves meticulously sealing the edges and seams. Proper sealing ensures a continuous and effective barrier against moisture infiltration. This process includes sealing seams and overlaps and securing the perimeter to create a seamless and robust protective layer.
Sealing Seams and Overlaps
Ensuring that all seams and overlaps are securely sealed is crucial for the integrity of the moisture barrier. This prevents any potential moisture from seeping through the joints where the barrier sections meet.
Applying Caulk or Sealant Along Seams and Overlaps:
- Select the Right Sealant: Choose a high-quality caulk or sealant specifically designed for use with polyethylene sheeting. Ensure it is compatible with the material of the moisture barrier.
- Apply the Sealant: Squeeze a continuous bead of caulk or sealant along the seams and overlaps where sections of the barrier meet. Use a steady hand to ensure an even application. This bead acts as an additional moisture barrier, filling any small gaps that might exist between the sheets.
Using Tape to Reinforce the Seals:
- Reinforce with Tape: After applying the caulk or sealant, use adhesive tape to reinforce the seams. Press the tape down firmly along the length of the seam to ensure a tight seal. The tape provides an extra layer of protection, securing the sealant in place and preventing it from peeling or lifting over time.
- Double-Check for Gaps: Inspect each seam carefully to ensure there are no gaps or loose sections. Reinforce any areas that appear weak or improperly sealed.
Sealing the Perimeter
The perimeter of the moisture barrier is equally important as the seams and overlaps. Proper sealing around the edges ensures that the barrier remains intact and effective.
Applying Sealant Around the Edges of the Barrier:
- Prepare the Perimeter: Ensure that the edges of the barrier extend slightly up the walls or any adjoining surfaces. This overlap helps create a more effective seal.
- Apply Sealant: Use the same high-quality caulk or sealant to apply a continuous bead around the entire perimeter of the barrier. Pay special attention to corners and any irregularities in the wall or floor surface. Apply the sealant generously to ensure complete coverage.
Ensuring a Continuous Moisture Barrier Without Gaps:
- Check for Continuity: Inspect the entire perimeter to confirm that the sealant forms an uninterrupted line around the edge of the barrier. There should be no breaks or gaps in the seal.
- Smooth the Sealant: Use a caulk smoothing tool or your finger to smooth out the sealant bead. This helps to ensure that it adheres well to both the barrier and the adjoining surfaces, creating a seamless and effective moisture barrier.
By carefully sealing the edges and seams of the moisture barrier, you ensure that it provides maximum protection against moisture infiltration. This step is critical for maintaining the integrity of the concrete floor and any subsequent flooring materials, helping to prevent damage and prolong the lifespan of the floor. Proper sealing creates a continuous, durable barrier that safeguards against the harmful effects of moisture, ensuring a successful and long-lasting installation.
Step 5: Inspect and Finalize the Installation
The final step in installing a moisture barrier for concrete floors is to thoroughly inspect the installation and ensure all elements are securely in place. This process includes checking for gaps and overlaps and reinforcing seals to guarantee a continuous and effective moisture barrier. Proper inspection and final adjustments are crucial for the long-term success of the moisture barrier.
Checking for Gaps and Overlaps
A meticulous inspection is necessary to identify any potential weaknesses in the barrier, such as gaps or poorly sealed overlaps.
Inspecting Seams and Edges for Complete Sealing:
- Thorough Inspection: Walk along the entire floor, closely examining all seams and edges. Look for any visible gaps, wrinkles, or areas where the sealant may have missed.
- Test the Seals: Gently press along the seams and edges to ensure the sealant and tape are firmly in place. Pay special attention to corners and transitions where the barrier may be more prone to gaps.
Addressing Any Missed Spots or Gaps:
- Mark Problem Areas: Use a marker or tape to highlight any areas where gaps or incomplete seals are found. This will help you easily locate these spots when applying additional sealant or tape.
- Apply Additional Sealant: Use the same high-quality caulk or sealant to fill in any gaps or missed spots. Apply a generous bead and smooth it out to ensure complete coverage.
- Retape if Necessary: If any seams appear loose or poorly taped, remove the old tape and apply a new strip. Press down firmly to ensure a tight bond.
Reinforcing Seals
Reinforcing the seals ensures that the moisture barrier remains effective over time, even in areas that may experience movement or stress.
Adding Additional Sealant or Tape if Necessary:
- Double Up on Seals: In areas with heavy traffic or where the barrier may experience more wear, consider applying an extra layer of sealant or tape. This additional reinforcement helps maintain the integrity of the barrier.
- Focus on Vulnerable Spots: Pay particular attention to high-risk areas such as doorways, transitions between different flooring types, and any penetrations through the barrier (e.g., pipes or conduits). These areas are more likely to develop issues over time and benefit from extra reinforcement.
Ensuring All Overlaps Are Properly Taped:
- Recheck Overlaps: Ensure that all overlaps between sections of the moisture barrier are securely taped. Overlapping sections should have a minimum of 2-3 inches of overlap and be thoroughly sealed with tape.
- Press and Smooth Tape: Use a roller or your hands to press the tape firmly along the overlaps, ensuring it adheres well without any bubbles or wrinkles. This step is crucial for maintaining a continuous moisture barrier.
By thoroughly inspecting and finalizing the installation, you ensure that the moisture barrier provides maximum protection against moisture infiltration. This careful attention to detail helps prevent potential issues that could compromise the barrier's effectiveness. A well-inspected and reinforced moisture barrier will protect the integrity of the concrete floor and any installed flooring materials, ensuring a durable and long-lasting solution.
FAQs
Contact Bull City Crawlspace Today!
Bull City Crawlspace will do everything we can to ensure your experience with us is excellent.
Request A FREE Estimate
Request a Free Estimate Form
Checkout Recent Post
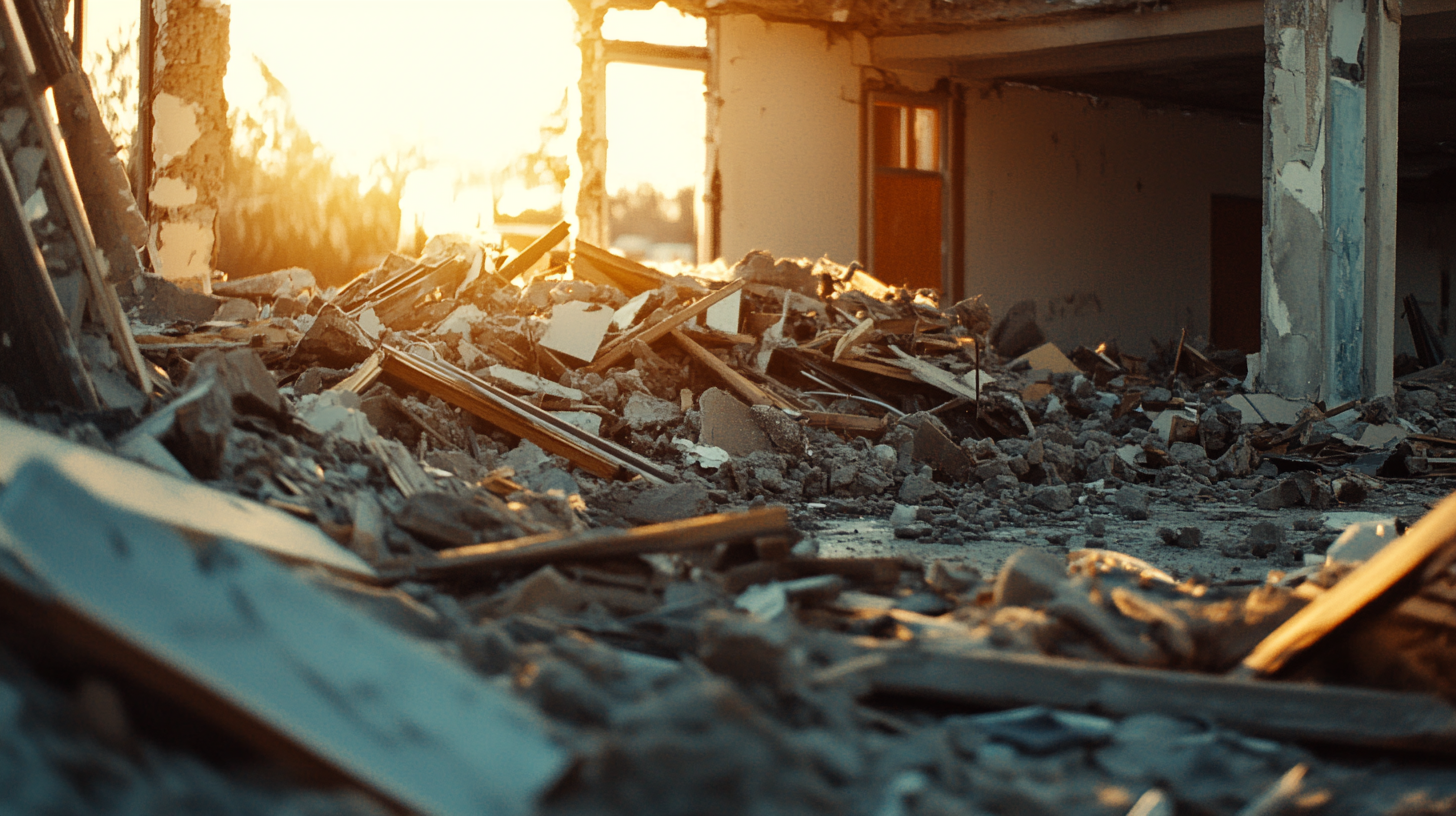
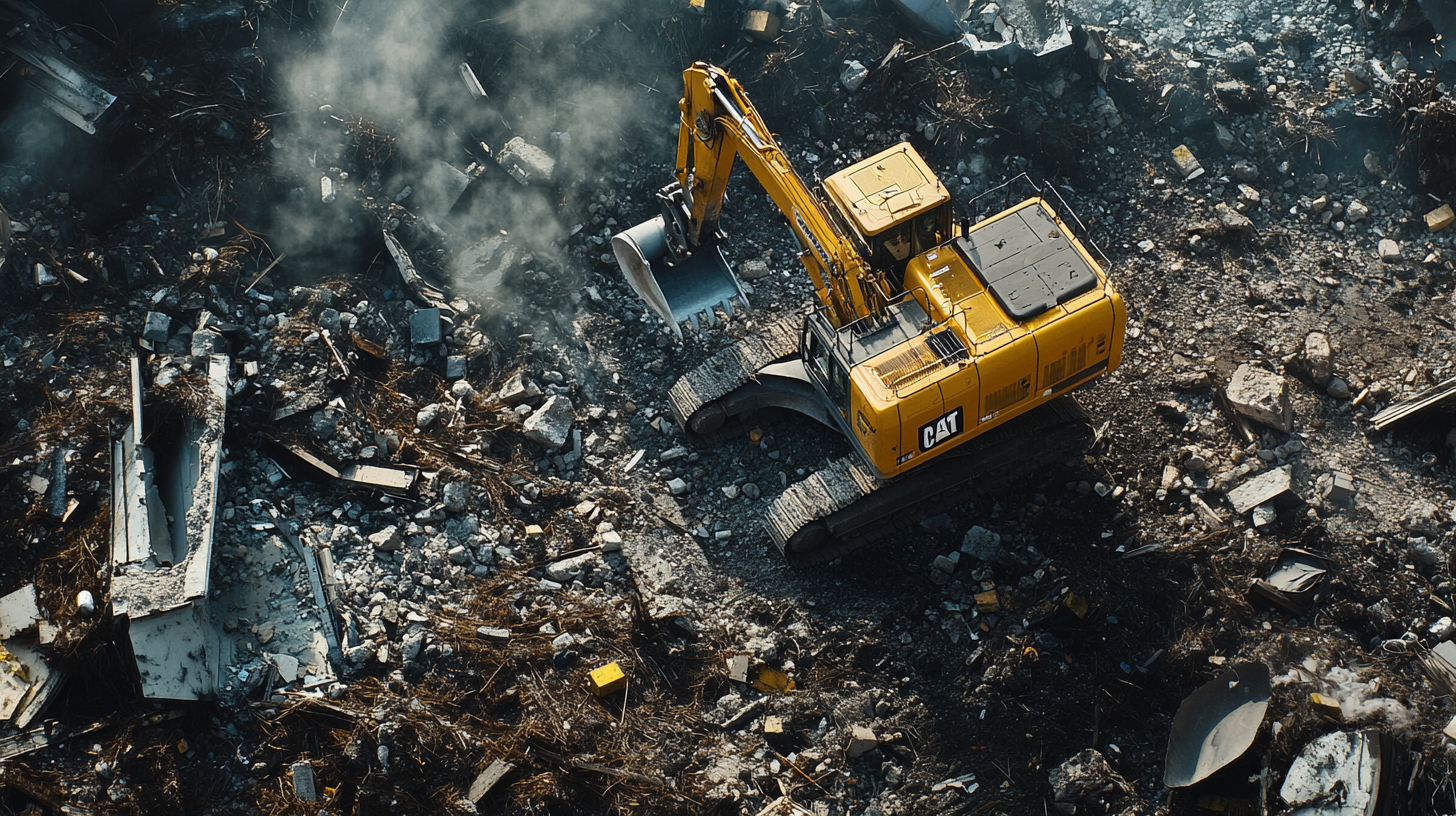


Got a Question? We’re Here to Help.
You can arrange an appointment or make an enquiry by phone or email, orget in touch to us via our contact form.